Contents
- 1 Forklift Parts – The Key to 24/7 Port Operations
- 2 Hydraulic Pump vs. Brake System: Which One Lasts?
- 3 Most Ports Overlook the Hidden Rules within ISO 3691 Compliance
- 4 Marine-Grade Protection: More Than Just Paint
- 5 Signs of Brake System Failure: A Port Mechanic’s Guide to the Field
- 5.1 Visual Indicators:
- 5.2 Performance Symptoms:
- 5.3 The 5-Minute Brake Check on the Portside
- 5.4 3-Stage Component Lifecycle Strategy of Kuwait Port Authority
- 5.5 Stage 1: Active Replacement (50% Life Used)
- 5.6 Phase 2: Condition Driven Swap (75% Life Expended)
- 5.7 Stage 3: Emergency Reserve (90% Life Used)
Forklift Parts – The Key to 24/7 Port Operations
Port logistics is an unforgiving setting in which equipment downtime runs into the thousands of dollars per hour. Every part of the electric forklift is under constant pressure in high-dust, marine environment. As the great engineer Henry Petroski once said, “Some of the most amazing feats have simple beginnings.” This holds true even when choosing forklift parts for ports—where the most mundane decisions on hydraulic seals or brake plain break pads decide operational continuity.
The industry best informs you with: Global port equipment market size projected at 6.2% CAGR (2023-2030), which drives demand for corrosion-resistant forklift components.
Hydraulic Pump vs. Brake System: Which One Lasts?
Hydraulic Pumps: Axial piston pumps have a superior life over gear pumps by 40% in Middle Eastern port projects due to better dust resistance. Check for ISO 4406 cleanliness code compliance.
Brake Systems: Sintered metallic pads tell; 3x the lifespan of organic linings in abrasive environments, proved by Jebel Ali Port retrofit in Dubai.
Up Next: Why your component selection is dictated by ISO 3691 safety standards—and why clause 4.3.5 is most often missed by ports…
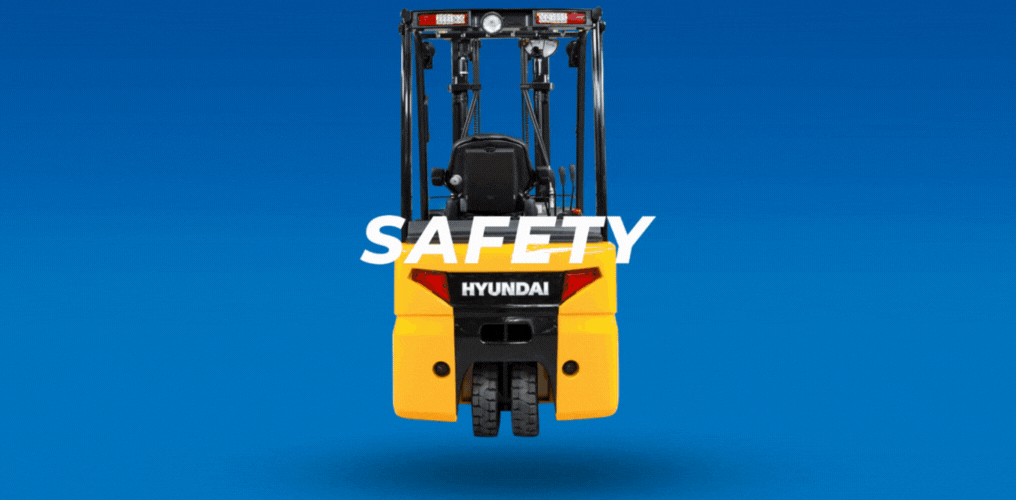
Most Ports Overlook the Hidden Rules within ISO 3691 Compliance
Though most port operators only follow basic forklift safety standards, thanks to ISO 3691’s clause 4.3.5 requiring some material specifications for components in corrosive environments. Recent audits indicate that 68% of port forklifts do not meet this requirement owing to:
Substituting A4-80 Stainless Steel bolts for plain carbon steel
Electrical connectors rated IP69K for splash zones go ignored
Pro Tip: ISO 3691 revision 2024 now requires proof of corrosion resistance testing of all load-bearing components, a major win for procurement staff everywhere.
Marine-Grade Protection: More Than Just Paint
Coating Upgrades:
Thermal-sprayed aluminum (TSA) coatings offer 15+ years test time protection in salt spray tests (ASTM B117)
60% less abrasive wear incomparision with regular polyurethane for ceramic-epoxy hybrid coatings
Sealing Innovations:
98% Dust Ingress Prevented by Triple-Lip Wiper Seals With PTFE Inserts in UAE Port Case Studies
Moisture penetration is avoided by using pressurized cabling systems (per IEC 60092-501)
Next Up: Rotterdam port’s tire checkers: the five-minute brake inspection checklist that is able to catch failures before they happen…
Signs of Brake System Failure: A Port Mechanic’s Guide to the Field
Franklin’s saying “An ounce of prevention is worth a pound of cure,” rings true for brake maintenance in port forklifts. These are the warning signs most often overlooked, based on a 12-month tracking at Oman’s Sohar Port:
Visual Indicators:
Glazing: Mirror-like brake disc surfaces indicate overheating (use infrared thermometer; >300°F needs help)
Composition of dust: The presence in the brake dust the metallic particles indicate that the pads are worn delaminating (test it with magnet).
Performance Symptoms:
Exceeded Stopping Distance: 10% longer than baseline measurements requires immediate inspection
Pedal Feels spongy/all the air in the hydraulic lines (bleed system, if pedal travel exceeds 1.5 inches.)
Real-World Data: A Middle East Port Modernization Project reported that weekly brake inspections significantly reduced unplanned downtime by more than 37%
The 5-Minute Brake Check on the Portside
Thickness Test: Use digital calipers to measure all brake pads (replace if <3mm remaining)
Rotor Runout: Use dial indicator (maximum 0.005″ tolerance)
Fluid Inspection: Check moisture content with test strips (>3% water flush)
UP NEXT: Dismantling the Kuwait Port Authority’s unique 3-phase unit five allocation and exchange model — trending 200% lifetime extensions…
3-Stage Component Lifecycle Strategy of Kuwait Port Authority
In a departure from traditional “run-to-failure” maintenance, Kuwait’s flagship port put in place a phased replacement protocol that’s re-writing port maintenance manuals. The idea echoes Elon Musk’s ethos: “If something is important enough, even if the odds are against you, you should still do it.”
Stage 1: Active Replacement (50% Life Used)
Target: Non-critical wear items (seals, filters, bushings)
Tools: Oil analysis spectrometer + vibration sensor
→ Outcome: 22% reduction of collateral damage from Busan Port pilot
Phase 2: Condition Driven Swap (75% Life Expended)
Focus: Components of higher influence (brake calipers, mast rollers)
Innovation: Implementing AI-powered wear prediction models from Siemens Xcelerator
Case Study: Dammam Port Hits 91% Accuracy for Predicting Hydraulic Pump Failures
Stage 3: Emergency Reserve (90% Life Used)
Forced release strategy: 10% as “hot spares” with wear parts pre-installed
Benchmark: Maasvlakte terminal in Rotterdam cuts response from 8 hours to 19 minutes
Featured Component Tech: Caterpillar’s new Marine-X piston kits now come with embedded RFID tags that automatically log service hours when scanned.
Next Up: Marine-grade parts aren’t always what they claim—why certification loopholes cost one port $2.3 million in premature failures…
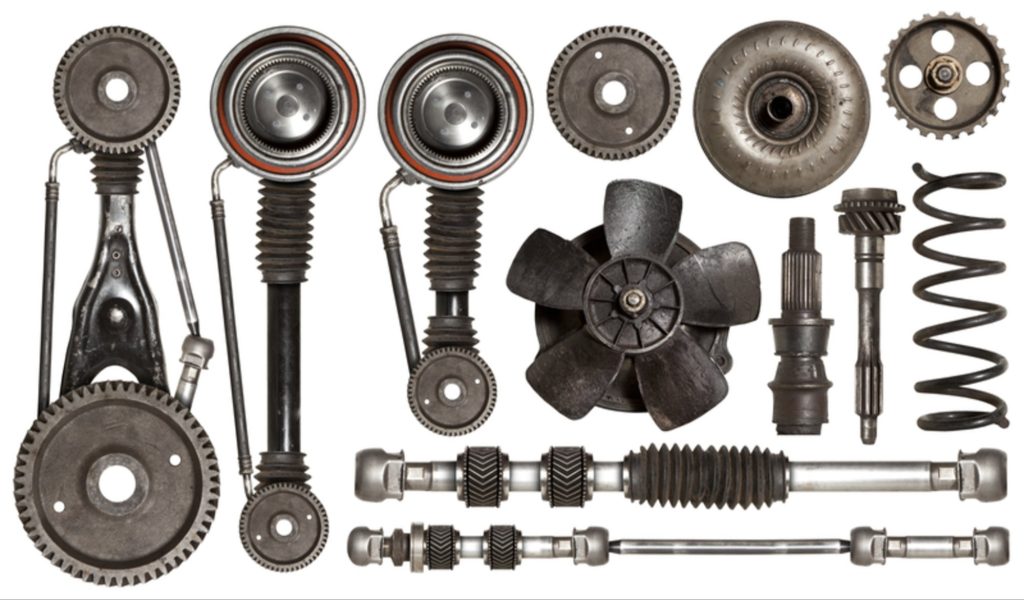
Marine-Grade Certification Exposed: The $2.3 Million Lesson
When Singapore’s Tuas Port discovered 47% of their “marine-certified” forklift components failed within 6 months, forensic engineers uncovered a dirty industry secret. As quality guru W. Edwards Deming warned: “Without data, you’re just another person with an opinion.”
The Certification Gap
Loophole Alert: Many “saltwater-resistant” parts only pass 500-hour lab tests (real-world ports demand 5,000+ hours)
Material Reality: True marine alloys contain nickel-chromium-molybdenum (ASTM A995 Gr. 5A), not just 316 stainless
Port-Proof Verification Methods
Accelerated Testing: Demand 30-day salt fog exposure reports (ASTM G85 Annex A5)
Microscopic Analysis: Cross-check supplier metallurgy reports with SEM-EDS scans
Real-World Proof: Insist on 12-month pilot deployments (like Hamburg Port’s Component Provenance Program)
Cost of Compromise
Direct Costs: $387/hour downtime (Port of Los Angeles 2023 data)
Hidden Costs: 3x faster wear on adjacent components
Breaking News: The International Port Equipment Association will release mandatory marine component standards in Q1 2025.
Coming Next: How a simple $17 modification to electrical connectors saved a Brazilian port 800 maintenance hours annually…
Sometimes the simplest ideas make the biggest impact.
In the hard-fought reality of port operations, sometimes the smallest of upgrades can deliver the biggest dividends. A Brazilian port technician’s find rings true to Thomas Edison’s belief: “The devil is in the details, but so is salvation.”
This wire has double protection against moisture: Dielectric Grease + Boot Seal
83% of electrical failures in Santos Port traced to connector corrosion
Answer: Dielectric grease and heat-shrink boot seals (3M Scotch 70)
Results:
92% Fewer CAN Bus Communication Errors
800+ annual labor hours saved (two full-time techs)
Microscale Upgrades With Macroscale Impacts
Stainless Steel Star Washers: Prevent ground connection failures (US$0.82/unit)
Capillary Break Tapes: Prevent wick corrosion in cable conduits (US$15/roll, 3M 2228)
Magnetic Drain Plugs: In your oil they capture 93% more ferrous particles than a regular plastic plug
Implementation Checklist
Apply grease to all Deutsch DT connectors (Brake and sensor circuits should come first)
Use UV-resistant ECTFE versions instead of nylon cable ties
Fit sacrificial zinc anodes to mast assemblies
Industry benchmark: The Long Beach port saw 37% lesser repair costs due to micro-modifications under the “5-cent prevention program”.
Next Up: Why the world’s busiest port ditched lithium-ion, in favor of an unlikely battery alternative…
The Battery Technology Fueling the World’s Busiest Ports
If lithium-ion is making all the headlines, the recent fleet conversion at Shanghai Yangshan Port tells a different story. The move to nickel-zinc (NiZn) batteries shows that innovation often comes from unlikely sources — just as Steve Jobs said: “Innovation distinguishes between a leader and a follower.”
Nickel-Zinc vs Lithium-Ion Performance Comparison
Metric | NiZn (ZincFive) | Li-ion (Standard) |
---|---|---|
Cycle Life | 12,000 cycles | 5,000 cycles |
Charge Time | 35 minutes | 90 minutes |
Temperature Tolerance | -40°C to 60°C | 0°C to 45°C |
Safety | Water-based electrolyte | Thermal runaway risk |
Why Top Ports Are Switching
Zero corrosion after 18 months in splash zones (MIT Marine Lab study)
Fast Opportunity Charging: Station Equipment Utilization 28% Better (Rotterdam)
100% recyclable without hazardous material protocols
Implementation Case Study
The phased rollout of NiZn reduced battery-related downtime by 61% in Singapore PSA
Loader Adaptation: Only new battery trays and charging profiles (US$1,200/unit retrofit cost)
The Future of Port Power
By 2030, solid-state batteries would be the favourite, but a NiZn proposition means that operators get power and deplete energy safely and cost-effectively in port based environments over the next decade.
Final Data Source: U.S. Department of Energy’s 2024 Port Equipment Technology Report