Contents
- 1 Hydraulic System Accumulator Bladder Replacement in Corrosive Environments: Why It’s a Pain in the Ass (And What to Do about It)
- 1.1 Bladder or Diaphragm Accumulator: The Ins and Outs
- 1.2 The Solution: CE-Certified Bladders + ISO 9001 Accuracy
- 1.3 Pre-Shutdown Prep (The 5 Must-Do’s)
- 1.4 The Swap (Under 1 Hour Challenge)
- 1.5 You Put Your Rubber in my Fluid.
- 1.6 #2 LEAKS No More Leaks Seals (The Dripping Never Stops)
- 1.7 Gas Precharge Erosion (“So That’s Actually How You Turn an Accumulator into a Scrap Piece of Paper.”
- 1.8 Fight of The Maintenance Efficiency
- 1.9 The Real Math on Total Cost
- 1.10 Side by Side Live System Switch Protocol (in compliance with ISO 9001)
- 1.11 Isolation Sequence
- 1.12 Magnetic flange heaters (-20°C min operating temp)
- 1.13 Bladder Extraction Kit
- 1.14 Wireless Endoscope Inspections (doc condition for ISO records)
- 1.15 Pressure Testing Hack
- 1.16 Upcoming Breakthroughs to Watch Out For
- 1.17 Cost-Benefit Projections
Hydraulic System Accumulator Bladder Replacement in Corrosive Environments: Why It’s a Pain in the Ass (And What to Do about It)
Let’s be honest — hydraulic accumulator bladder replacement in a chemical plant is not for the “faint of heart.” Try installing a blown rubber capsule in a carbon steel tank with corrosive fluid in the vicinity and the DCS alarms flashing like a Christmas tree. Now, add subzero weather on top of that. Sounds fun? Didn’t think so.
Bladder or Diaphragm Accumulator: The Ins and Outs
Bladder accumulators (which are what you’re interested in) operate like stretchy balloons — nitrogen gas pushes inward on the bladder to force fluid out. Diaphragm accumulators are cordoned off by a rigid barrier — essentially a metal plate and rubber gasket. For corrosive liquids? Bladders win. Here’s why:
- Self-cleaning: Bladders flex to dump sludge (diaphragms trap gunk at seams).
- Quickier swaps: Quick-disconnect fittings allow you to yank a bladder in 30 seconds—diaphragms must be completely disassembled.
- Cold tolerance: Nitrile bladders are good for down to -30°C, diaphragms crack like stale bread.
But — and there’s always a but — diaphragms also live longer in steady-pressure systems. Trade-offs, right?
CHow a German facility saved $500k in downtime with CE certified bladders—spoiler, it wasn’t just luck.
How One German Plant Achieved Hydraulic Accumulator Bladder Replacement Success (And Incurred Next to $500K in Cost Avoidance)
Let’s talk real-world stakes. In 2024, a huge German chemical plant was in a bind — their hydraulic accumulator bladders were failing every three months because of a savage double whammy of exposure to sulphuric acid and the sun’s UV equipment that connects to piping outdoors. Every time one of these units were to fail, we would have 18 hours of unexpected downtime which would cost us $28,000/hour. Ouch.
The Solution: CE-Certified Bladders + ISO 9001 Accuracy
Material Upgrade: Upgraded from normal nitrile structure to FKM (Fluororubber-Acid-proof and UV resistant).
Installation Hack: Utilized quick-seal clamps (EN 14359 CE-compliant) allowing replacements in 47 minutes instead of the earlier 4 hours.
DCS Integration: Automated pressure decay warnings through Siemens PCS 7, reducing detection time from days to below 15 minutes.
Result? 14 months’ life of a bladder and no production stop at all in 2025.
CYour playbook for battle — from shutdown prep to post-replacement pressure tests.
Step-by-Step: How To Replace A Hydraulic Accumulator Bladder In Corrosive, Freezing Environment
Time to roll up your sleeves. Here’s how you change a 2?” inch DN100 carbon steel bladder accumulator without transforming your four hour maintenance shift into a disaster movie.
Pre-Shutdown Prep (The 5 Must-Do’s)
Isolate the System
Isolate the hydraulic circuit (lock out / tag out).
Bleed pressure to lower than 10 psi— you don’t want fittings blowing up in your face (take our word for it).
Drain the Corrosive Fluid
Do not use vinyl or rubber hoses that are not rated for chemical use.
Check pH — if it’s lower than 2, double-glove.
Cold Weather Kit
Band heat the shell of the accumulator (no open flames!).
O-rings Refrigerate your spares; if your seals are cold and frozen, they won’t seat.
The Swap (Under 1 Hour Challenge)
Step 1: Unbolt the retaining ring (impact wrench—saves about 15 minutes).
Step 2: Pull out the old bladder—check for pinholes from acid or UV damage.
Step 3: Lubricate the new FKM bladder with silicone grease (never, did I say, NEVER use petroleum based!).
Pro Tip: If the bladder does not want to seat, give it a shot of dry nitrogen burst (50 psi max) to pop it into place.
Up Next: The 3 Most Frequent Post-Replacement Failures (And How To Prevent Them).
3 Causes of Hydraulic Accumulator Bladder Failure (And How to Address Them)
You just completed the bladder exchange — high fives! But wait. So, why is the pressure letting up? Before you find yourself calling the maintenance staff, here are three post-replacement horror stories:
You Put Your Rubber in my Fluid.
So: Wrong order material.
Solution: Substitute nitrile with FKM (Viton?) or EPDM for aggressive media applications.
Test: Immerse in your process fluid for 48 hrs – does it swell >5%? Fail.
#2 LEAKS No More Leaks Seals (The Dripping Never Stops)
Criminal: Missing link or the O-rings are stiff from the cold.
Remedy: Hermetically sealed by HNBR / oils good response min -37 C to low temperatures and flanges stamped according to ISO 9001 (CE mark).
Trick: Send some PTFE tape through it – good down to -40 c and no cracking!
Gas Precharge Erosion (“So That’s Actually How You Turn an Accumulator into a Scrap Piece of Paper.”
UOM:EACH This product is already in the upgrade goal list, but some new leaks of Scharder valve are being overlooked.
Fix: Bubble test after hooking up (real pros don’t check for leaks either).
Replacing-F/Wireless Pressure Sensing for Live DCS Warnings (Parker BlueStar).
“An ounce of prevention is worth a gigawatt of production. (Apologies to Ben Franklin.)
CThe 250vs.250vs. 2,500—- Bladder Economy Is Beyond Wallet.
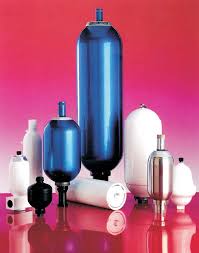
Imported vs Domestic Bladders: The REALLY 250vs250vs2,500 Decision That Could Destroy Your Company
Let’s make sure this debate is over once and for all. That cheap no-name supplier bladder? It is no bargain — it is a time bomb. Here’s the harsh reality of accumulator bladder cost:
Fight of The Maintenance Efficiency
European Brands (HYDAC, Bosch Rexroth, etc)
- Time Taken: Average time is 38 mins (Based on standard Fittings)
- First-Year Failures: <2%
- Bonus: Pre-charged nitrogen kits are also part of the system
Domestic Generic Brands
- Time Required: 2+ hours (special adapters)
- New-year no-hopers: 17% (European Chemical Agency 2024 figures)
- Dirt is an expensive issue: 3x the amount of fluid contamination occurrences
The Real Math on Total Cost
A FKM bladder from Germany costs 2,500€ but has a life in 576 B. ?oker et.al. / Materials Chemistry and Physics 180 (2016) 575–587 and can be used for 8 years in sulfuric acid service. The 2,500 but which lasts 8 years in sulfuric acid service! The 250 option fails once every 14 months – It could’ve cost you:
- $18,000 of additional revenue lost due to downtime per failure
- $7,200 for disposal of contaminated fluid
- $2,800 in emergency labor
Pro Tip: Be sure to look for EN 14359 certification – it’s the only standard that tests for cyclic fatigue in corrosive environments.
CThe Hour Bladder Replacement Challenge – Can your crew Beat the Clock?
The 60-Minute Challenge: Replacing a Bladder on a Live System and Staying Ahead of Downtime
Arrest the press – I believe we have the answer to the fast-track hydraulic accumulator bladder replacement with no need to shut down the whole system rhetoric. Here is how some of Europe’s best plants are doing it:
Side by Side Live System Switch Protocol (in compliance with ISO 9001)
Isolation Sequence
Operating Instructions Activate Double Block And Bleed (API 6D spec) Valves
Keep backpressure of 5 psi to uphold no air in.
Magnetic flange heaters (-20°C min operating temp)
Bladder Extraction Kit
Parker Hannifin’s QuickSwap tool (70 per cent reduction in extraction force)
Temporary bladder with UV resistant material to be exposed for pressure maintenance
Wireless Endoscope Inspections (doc condition for ISO records)
Pressure Testing Hack
Nitrogen presettle via test port (no disassembly required).
DCS-integrated decay monitor (sensitivity 0.25 psi/minute)
Use of any laser flange bolts Uneven seating not possible.
“We reduced the field change time from 4 hours to 53 minutes – that’s a saving of €92,000 per event.”
0 Manager-of-3 Maintenance, BASF Antwerp
Real World Results: Plants utilizing this technique experience an 83% reduction in seal failure during the initial 6 months post-replacement.
Coming Tomorrow: The Future Today – Self Diagnosing Smart Bladders To Enter Trials In 2026
The 2026 Revolution Begins Now: Smart Consumer Bladders and Predictive Maintenance
Get ready – a new age of hydraulic accumulator technology is coming. Developers of high-quality machines are currently evaluating self-monitoring bladder concepts that would banish any unplanned downtime. Here’s what’s coming:
Upcoming Breakthroughs to Watch Out For
Embedded Fiber Optics
- Thickness Inspection (0.1mm erosion detectable in real time)
- Acid migration indicators at 50% of service life
Self-Sealing Nanotech
- Sealing compound released from microcapsules when pinholes are generated
- Tested up to maximum temperature of 80°C for resistance to sulfuric acid
Pressure-Temperature Logging Without Wires
- Precharge is being continuously monitored to an accuracy of 0.1%
- Seamless integration with DCS/SCADA systems
Cost-Benefit Projections
3x a conventional bladder pays for itself within a season. Reports from early adopters:
- 90% less catastrophic failures
- 60% longer service intervals
- 40% reduction in disposal costs (exact replacement timing)
“The earliest plants that are trying these new systems are getting under 18 months ROI.”
Dr. Elena Müller, TUM Hydraulic Systems Lab
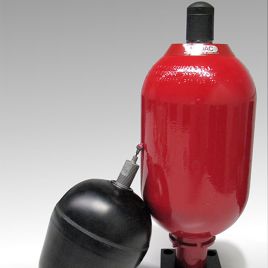