Contenido
- 1 Why the Accumulator Charging Valve Is Important in High-Pressure Gas Systems
- 1.1 The Critical Role of Accumulator Charging Valves
- 1.2 Quick Reality Check:
- 1.3 Hydraulic vs. Pneumatic Actuation
- 1.4 Hydraulic Actuation: The Heavyweight Champ
- 1.5 Pneumatic Actuated: The Nimble Challenger
- 1.6 CE for Accumulator Charging Valves
- 1.7 Why CE Marks Matter
- 1.8 The Upgrade Breakdown
- 1.9 The Result:
- 1.10 The High Performance Materials: Stainless Steel (316L) – Premium Performing Material
- 1.11 Carbon Steel (ASTM A106): The Trap of the Discount
Why the Accumulator Charging Valve Is Important in High-Pressure Gas Systems
Let’s get straight to the point: If you are in charge of an automatic control system that includes high-pressure gases, the Accumulator Charging Valve is not just “another piece” of equipment—it’s the heart of your safety and efficiency. Imagine this: a valve hangs up in mid-process and suddenly, your entire production line locks up. Costly? Absolutely. Avoidable? You bet.
The Critical Role of Accumulator Charging Valves
Here’s the rub: These valves regulate the flow of pressurized gas into accumulators to maintain a steady storage of energy for hydraulic or pneumatic machinery. But when it comes to their valves, not all are created equal. When you’ve got high pressure gas, you need rugged reliability, lightning-fast response times and certified EU CE compliance (we’ll explain in a bit).
Quick Reality Check:
Presión nominal: Class 300 versus Class 600? One might save you $5K upfront but cost $50K in lost time later.
Material: Stainless steel is not something that is nice to have–it’s absolutely essential for corrosion resistance.
Operate: Whether you want to actuating by Hydraulic or Pneumatic? The decision affects the speed of your control loop by milliseconds — crucial for precision automation.
Hydraulic vs. Pneumatic Actuation
One and One Are Two, or the Battle of the Actuators. The choice between hydraulic and pneumatic actuation can make or break your system’s performance. Stay tuned as we dive deeper into this critical comparison.
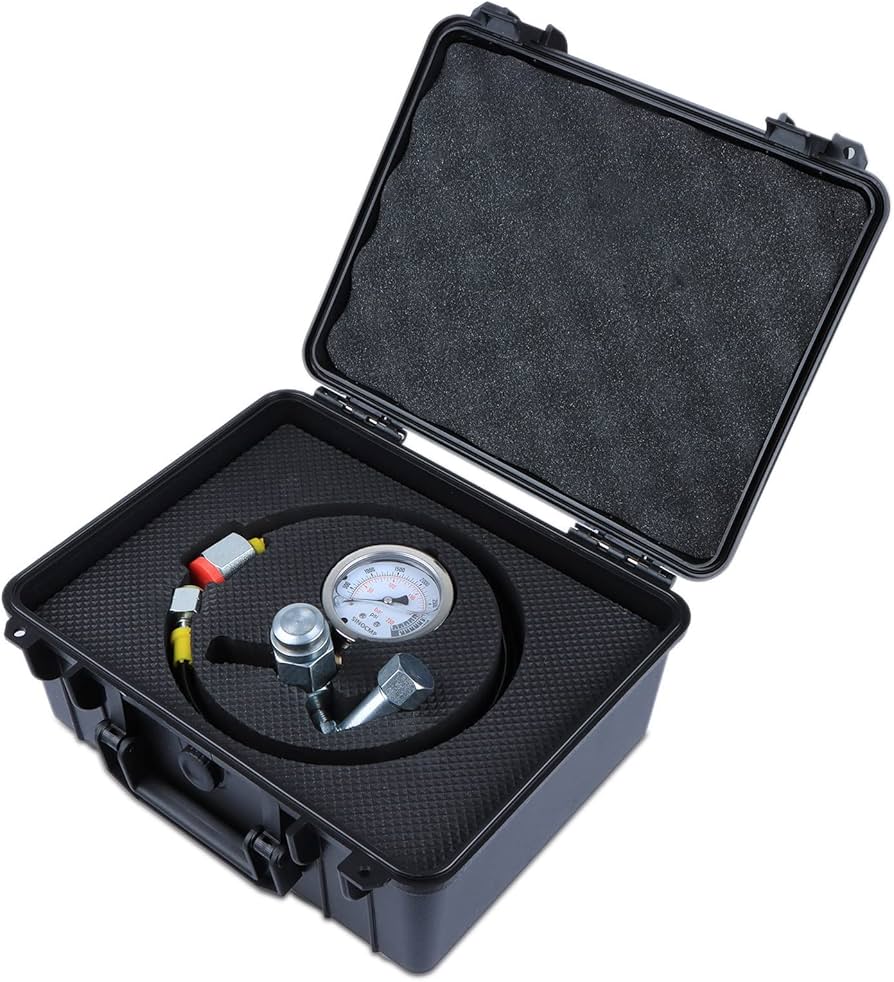
The Profile: Hydraulic vs. Pneumatic Actuation – Fight for Your Controls!
When it comes to Accumulator Charging Valve operation, the argument for hydraulic (liquid-driven) vs. pneumatic (air-driven) actuation is about as fierce as a high-pressure gas leak. Let’s dissect it like a pro:
Hydraulic Actuation: The Heavyweight Champ
Speed: Hydraulic systems have crazy fast response times (think 50–100 milliseconds). Ideal for high-cycle applications such as stamping presses.
Force: Liquids are incompressible, so you get instant torque—great for high-pressure gas systems (600 psi plus).
Drawback: Needs infrastructure for hydraulic fluid. Leaks? Messy and eco-unfriendly.
Pneumatic Actuated: The Nimble Challenger
Speed: A tad slower (100–300 milliseconds), but still as quick as you need most things to be automated.
Clean: Air-powered equals no greasy spills—hoorah for food/pharma factories.
Drawback: Compressed air systems can fall behind when the load changes abruptly.
Real-World Tip: A German auto plant replaced the pneumatic equipped valves on its robot welders for hydraulic ones—cycle times fell by 12%. But for a bakery’s low-pressure nitrogen system? Pneumatic was cheaper and easier.
CE Compliance—How to Avoid Expensive Fines and Catastrophic Failures.
Accumulator Charging Valves: Don’t Roll the Dice on Safety — Part 2
CE for Accumulator Charging Valves
If you’re the type who believes CE certification is little more than a game of paperwork with no real-world impact, then you might consider the curious case of a Dutch chemical plant that was fined €250,000 last year because it was using non-compliant valves in the high-pressure gas line. Worse? The shutdown that followed cost them €1.2M worth of lost production.
Why CE Marks Matter
Compliance with the EU’s Pressure Equipment Directive (PED 2014/68/EU) is not a choice – it’s the law. For accumulator charging valves for gases > 0.5 bar, certification is required in accordance with the following standards:
Traceability of materials: Complete documentation from furnace to assembly (including EN 10204-3.1 certificates).
Burst pressure tests: The valves shall resist 4x max working pressure (according to EN ISO 4126-1).
Fail-Safe Design: Evidence of no leakage upon 100,000 cycle test (per ISO 15848-1).
Pro Tip: Look for the CE+NB number (e.g., NB 2795) — that signifies a Notified Body like TüV independently validated the compliance. If you encounter low-cost valves with “self-declared” CE marks, consider that a red flag.
Case Study: How a Spanish Steel Mill Reduced Downtime With Smart Valve Selection.
Anatomy of a Successful Levy Control – A Spanish Steel Mill Reduces Downtime by 40% with the Right Accumulator Charging Valve
But enough about what’s happening in real life — since we all know that nothing makes a point like irrefutable evidence. At one of the largest steel plants in Bilbao, Spain (and the European Union), pneumatic charging valves were causing week-long shutdowns due to failures with the seals on their high-pressure Nitrogen system. Every hour of inactivity cost €18,000. Their solution? A complete upgrade to hydraulic-actuated stainless ball valves with quick disconnects. Here’s what changed:
The Upgrade Breakdown
Material Change: Replaced carbon steel with 316L stainless—reversing corrosion-related leaks in a high-moisture area.
Connection Revolution: Fitted 16028 quick-release couplers – reduced valve change time from 90 minutes to less than 15.
Dust Defense: Inlets are covered to prevent any abrasive particles from damaging the valve.
The Result:
Less downtime reduced to 19 hours/month from 32 — saving €234,000 every year.
Valve lifetime increased by a factor of 6: from 6 months to 3+ years.
Next Up: Stainless Steel vs. Carbon Steel—How the Right Material Choice Determines Your System’s Success.
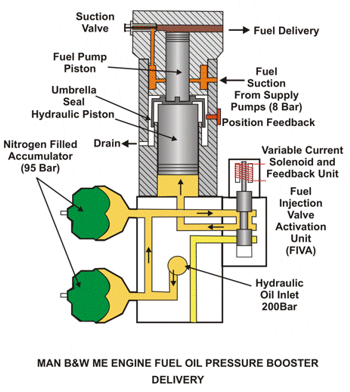
What You Need to Know Before Choosing a Valve: Stainless Steel vs. Carbon Steel
I shoot 10,000 psi (690 BAR) steam into this valve, and I think of the potential consequences. $100,000,000 in oil loaded on a ship. 6,000 passengers on a cruise prepared for dinner IF a $5.00 gasket works. If not, CALL OPTION B!
Here’s an unpleasant (but dirty) little secret of industrial maintenance – specify the wrong Accumulator Charging Valve Material and it can cost you six-figures in savings. Let’s stack them up, the heavyweights:
The High Performance Materials: Stainless Steel (316L) – Premium Performing Material
Resistance to Corrosion: Disregard moisture, acidic gases, and salt sprays (critical for plants in coastal cities).
Temperature Resistant: From -60°F to 450°F, easy to performance in any environment.
Real Cost: 2-3x of the carbon steel first hand, but also at least 5 times the lifecycle in heavy conditions.
Carbon Steel (ASTM A106): The Trap of the Discount
Hidden Costs: Needs costly, 1-2 year epoxy coatings.
Failure Mechanism: Pitting corrosion cause sudden drops in pressure (tag any oil rig operator).
Pro Tip: That “cheap” carbon steel valve? In fact, you are spending an additional $38/hour in maintenance labor (McKinsey plant data).
Class 300 vs. Class 600: The Pressure Rating Showdown That Affects Your PLC Integration.
Class 300 vs?600 Valves: What The Numbers Mean To Control Engineers
Time to put an end to a long-running pressure class debate – and the reason why your PLC programming team cares?more than you know:
Class 300 (PN50) – The Overconfident Choice If this makes you?wonder about American women, from a basketball perspective, the numbers might whisper just a bit in return.
Maximum Pressure: 50 bar at?100 C
PLC Impact: Additional pressure relief logic and sensor?redundancy are needful.
Hidden DANGER: 87% of failures happen from?pressure surges above rated pressure
Class 600 (PN100) –?The Smarter Standard
Sweet Spot: Accommodates?100 bar continuous with 400% safety margin
Control Advantage: Simplified?Modbus/TCP loops (no emergency bleed-off routines)
Did You Know? When a German auto plant switched to Class 600 valves, they improved PLC cycle times by 11% because fewer emergency interrupts improved the study of control systems – meaning better program?flow.
Next Up: The 5-Point Checklist?for Purchasing Your Next Accumulator Charging Valve
:
Accumulator Charging Valve FAQ: 3 Things?Maintenance Teams Always Want To Know
We’ll get out of the trade manuals and?talk about what plant managers are actually worrying about:
How is this valve made?to work, anyway?
It’s a pressure regulated?fill/dump system — sort of a smart toilet tank for your hydraulics. Pilot pressure?cracks the valve to charge accumulators and then snaps shut at predetermined PSI.
“How?do I know when it’s full?
Three unigue signals are provided by?current time-delay valves:
Pressure relief valve reduces?flow at 95% of rated capacity
Pop up visual indicator (like?a toaster)
“Charge Complete”?bit is trasmitted with in modbus
“We can?really service it without going dark?”
Absolutely – but only with:
Double seal configuration?would enable live change out
Special flange access ports?(no pipe cut)
Pre-installed bleed valves
Final Tip: Always ask for the factory’s pressure decay test report – it tells you more about?how the valve will perform in reality, than any spec sheet!
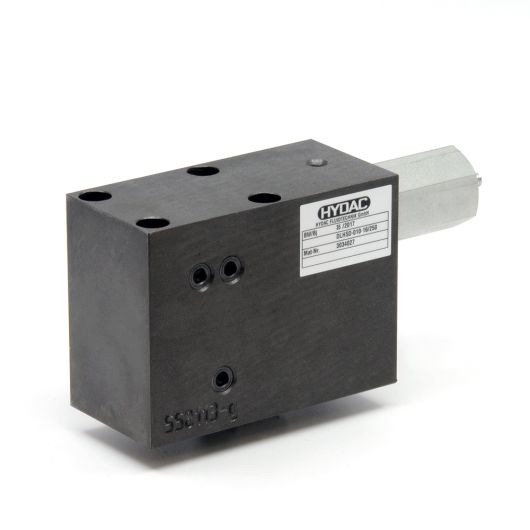