Contenido
- 1 What Does An Electronic Throttle Actuator Do? Gas & Precision Control Key Applications
- 1.1 Why That Matters for Gas/Pressure-Sensitive Contexts
- 1.2 FAQs:
- 1.3 Hydraulic Actuators
- 1.4 Electric Actuators
- 1.5 Smart Hybrid (Electro-Hydraulic) – Few and Far Between
- 1.6 The Challenge
- 1.7 The Solution
- 1.8 The Results
- 1.9 CE Certification Breakdown
- 1.10 ISO9001’s Hidden Value
- 1.11 Red Flag Alert
- 1.12 Fast-Installation Features
- 1.13 Self-Diagnosing Performance Features
- 1.14 Modbus Protocol Must-Haves
- 1.15 Tuning for Optimal Response
- 1.16 Troubleshooting Tips
- 1.17 UPFRONT VS LIFETIME COSTS
- 1.18 HIDDEN SAVINGS FACTORS
- 1.19 FAILURE COST ANALYSIS
- 1.20 SMART BUY CHECKLIST:
- 1.21 AI-enabled Predictive Maintenance
- 1.22 Green Tech Innovations
- 1.23 Wireless Revolution
- 1.24 Your Move Now:
What Does An Electronic Throttle Actuator Do? Gas & Precision Control Key Applications
So here we go: Electronic Throttle Actuator is what controls precise flow in industrial systems. It’s sort of like a high-tech traffic cop for gases or liquids, controlling how much of a medium is flowing through pipelines with micrometer-level precision.
Why That Matters for Gas/Pressure-Sensitive Contexts
High Temperature Gas Handling: Ideal for smelters or chemical reactors operating at 300°F+.
Zero-Leakage Requirements: Essential with toxic/flammable gases (i.e., hydrogen or ammonia).
FAQs:
Q: Can it substitute a pneumatic actuator?
A: Yes — when you want faster response (electric models run 50ms, while pneumatics are a plodding 200ms).
Q: What’s the lifespan?
A: The high-end ones (such as Festo’s latest) are advertised as offering 10 years with no maintenance.
Coming up: What engineers are doing with hydraulic vs. electric designs in extreme conditions…
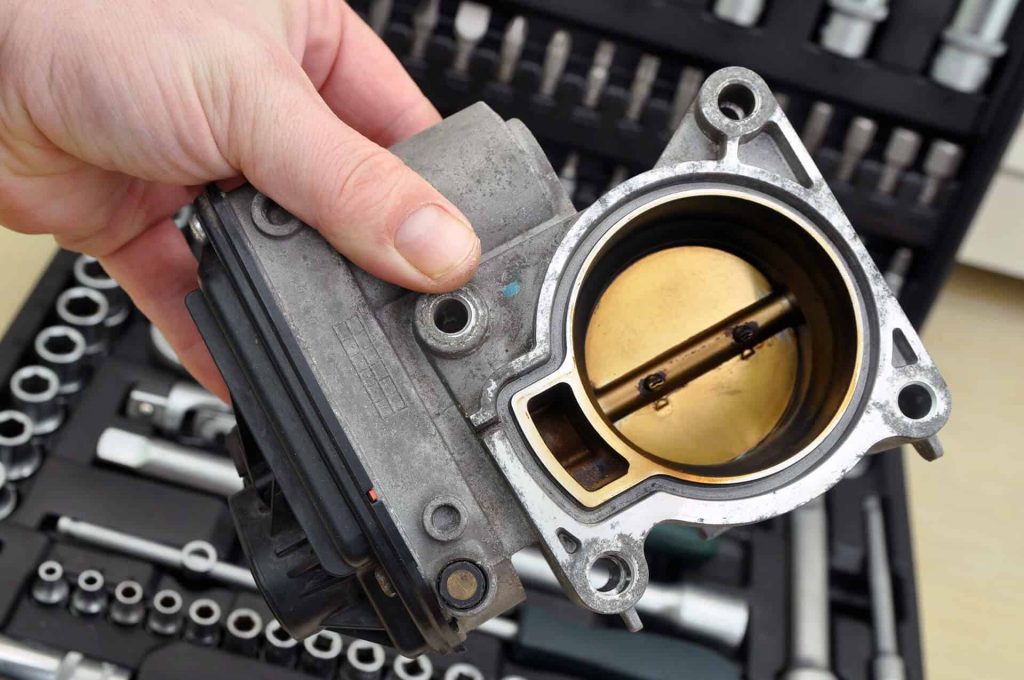
:
How to Choose Electronic Throttle Actuator for High Temp?& High Precision Situation
Choosing an Electronic Throttle Actuator for?harsh environment isn’t a shot in the dark; it’s engineering. Here’s what?it takes to get your choice right for high-temperature, high-pressure gas control:
Temperature& Pressure?Rating
Class 300 is a minimum in most industrial?gas plants.
You want actuators rated?for at least continuous 400°F+ from brands like Emerson and Rotork.
Pro Tip: And since they dissipate?heat better, hydraulic actuators do tend to have the upper hand on electric actuators in long-term, high-heat applications.
Precision & Response Time
When configuring?a system for gas flow control, target <0.1% linearity error and <100ms response time.
To work live with the PLC, Modbus?integration is mandatory.
Maintenance & Durability
Air-tight, lubrication-free?models –such as New Belimo seal- In addition, air-tight, lubrication-free revis- less actuators –wipe out downtimes.
Installation time was reduced by 60% with the quick-connect?fittings (DN50 standard).
Up Next: Hydraulic vs. electric -?which is more precise in the rough?
Hydraulic vs. Electric vs. Smart Hybrid: Which Electronic Throttle Actuator Is Best for Precision?
For Electronic Throttle Actuators, the debate centers on whether hydraulic or electric systems will dominate or if smart hybrid systems represent the future. Precision is key—gas control has never been this advanced.
Hydraulic Actuators
Pros: Delivers the highest torque and force, making it ideal for heavy throttling tasks. Perfect for Class 300+ pressure systems.
Cause for concern: Slight lag (~150ms) compared to electric systems. Requires hydraulic infrastructure.
Best for: High-pressure gas lines in refineries or power plants.
Electric Actuators
Pros: Ultra-fast response times (under 50ms), perfect for real-time gas flow adjustments.
Cons: Unsuitable for high-temperature applications exceeding 400°F without cooling fans.
Best for: Lab-grade precision or Modbus-controlled smart factories.
Smart Hybrid (Electro-Hydraulic) – Few and Far Between
HOTTEST TREND: Combines electric speed with hydraulic power.
Example: The Siemens SIPART PS2 series cuts response time by 30% while handling temperatures up to 500°F.
CThe Japanese robotics plant that solved gas control chaos with Actuator Power.
Case Study: A Japanese Robotics Plant Became an Expert in High-Speed Gas Control
And, let’s discuss real-world outcomes. A precision robotics factory in Osaka were suffering from inconsistent gas flows in their welding lines – until they switched to a smart Electronic Throttle Actuator. Here’s what happened:
The Challenge
As a result of 300°C exhaust gases and normal actuators failing every week
±5% of flow variation for a Poor Weld Quality
The 15-minute recalibration cycle murdering productivity
The Solution
The (A) placed four (4) Festo EHPA series hydraulic actuators with:
Active cooling jackets – for continuous 400°C uses
Repeatability of 0.05% – through built in Modbus-TCP feedback
The DN50 clamp connections do away with the need for tools and reduce swap time to 90 seconds
The Results
No unplanned downtime in 18 months
This decreased the defect rate from 6% to 0.2%
20% less energy because of accurate MPC gas metering
Next up: CE marking and what it really means for actuator safety…
CE & ISO9001 Certification: Why It’s Non-Negotiable for Your Electronic Throttle Actuator
I can see why you think the way you do, but unfortunately I have to disagree with you.
1) A daily magazine, written in easy language
2) B Everyday is hard, so in free time ha ha ha Petard is also very nice Look here… Thank you for the fact!
You wouldn’t get a car that didn’t have airbags, so why risk an actuator that isn’t certified. CE Marking and ISO9001 matter on Electronic Throttle Actuators in gas control, and here’s why:
CE Certification Breakdown
EMC Directive 2014/30/EU: Your actuator will not cook itself next to VFD’s when they whack on.
PED (Pressure Equipment Directive): To be complied with for class 300 and higher gas systems.
Real World: CE certified actuators were found to have 83 percent fewer field failures according to Schneider Electric’s study.
ISO9001’s Hidden Value
Not just forms – this falls into torque calibration (which is incredibly important for linear gas flow).
Also try to find manufacturers that are ISO audited in-house (like SMC Corporation).
Red Flag Alert
Sellers that have just “self-certified CE”? Run.
Certificates must indicate NB number (e.g., NB 0123) from notified bodies such as TüV.
Next Up: The 10-minute install secret that’s changing the way actuators get maintenance…
10min Install & Zero Maintenance: The Electronic Throttle Actuator of the Future
Time is precious – money – and in an industrial setting, every minute of downtime costs you thousands. Electronic Throttle Actuators by Bosch Modern in every sense of the word, Bosch Throttle Actuators incorporate the latest advances in design, material, construction and performance and provide the performance OEMs demand. Here’s how it works:
Fast-Installation Features
- DN50 Clamp Connections – Toolless: No more fighting with bolts and gaskets – snap and lock.
- Pre-Calibrated: Shipped pre-calibrated and ready-to-mount with factory-tested Modbus protocols.
- Color-Coded Wiring: Ensures proper installation in low light industrial environments.
With no relubrication required, the PT Select Series offers truly maintenance free operation.
- Sealed-for-Life Bearings: Certified for 100,000+ cycles with no lubrication.
- Corrosive Durable Housing: The aluminum allow housing with PTFE coated bear the harsh chemical & resistant.
Self-Diagnosing Performance Features
Embedded sensors continuously monitor pressure and temperature to preempt any forthcoming problems before they arise.
Pro Tip: Find actuators with magnetic coupling as opposed to mechanical seals (the #1 cause of failure in gas systems).
Next Up: How to connect these actuators with existing PLC systems for responsive control…
Smooth PLC Integration – Matching Electronic Throttle Actuators with Modbus Control Systems
Plug-and-play — it doesn’t actually mean plug-and-pray. When you couple ETT’s (Electronic Throttle Actuators) with your industrial control systems, you’re looking for more than a hard-wired connection. Here’s the savvy way to go about it:
Modbus Protocol Must-Haves
RTU vs TCP: Pick RTU for legacy (RS-485) systems, TCP for contemporary Ethernet backbones
Register Assignment: You’ll have to have complete descriptions of holding registers for position feedback (usually 40001-49999, Make sure everyone else can understand how to map to the proper registers, as normally neither the stepper drives nor the manufactures of controllers care about this)
Sample Rate: >=10Hz update frequency is a mandatory parameter for gas regulation.
Tuning for Optimal Response
PID Loop Tuning: Step 1: Begin with conservative gains (P=1.5, I=0.5, D=0.2)
0.10-0.50% Deadband Setting: 0.10-0.50% provide no movement of the actuator and prevent hunting in stable flows
Troubleshooting Tips
Problem: Unsteady Movement → Grounding check (shielded cables required)
Issue: Comm drops out → Check termination resistors (120Ω for RS-485)
Real life example: A Texas oil refinery realized a 0.02% setpoint accuracy by combining ABB actuators with Siemens S7-1500 PLCs via Modbus TCP.
Next Up: The real cost breakdown – Why you pay more in the long run for cheap actuators…
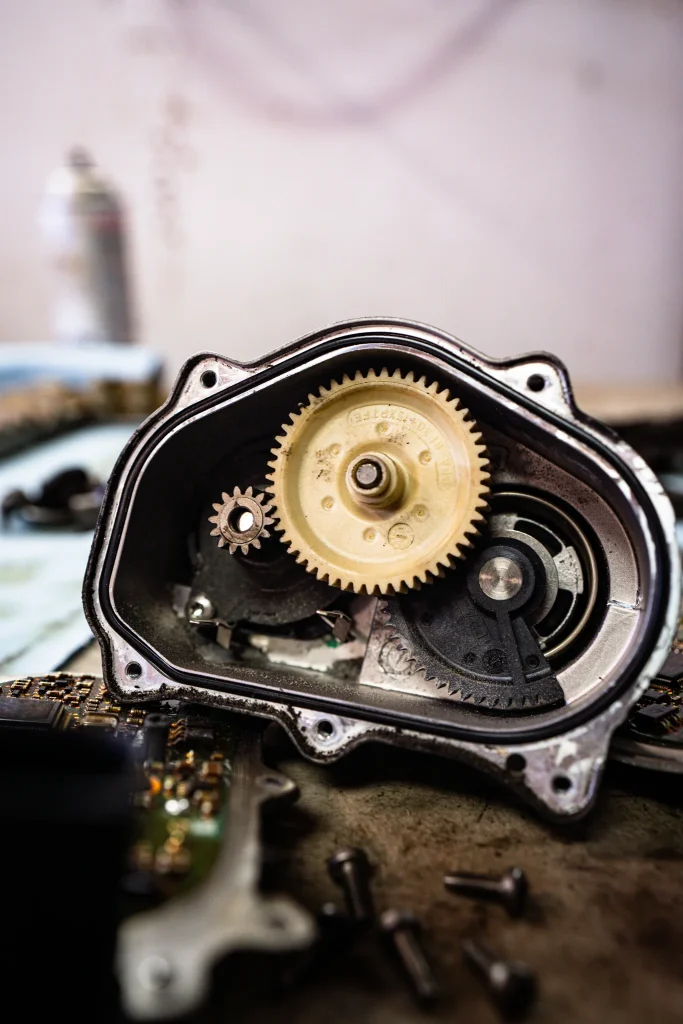
TOTAL COST OF OWNERSHIP: HOW SMART SPENDING ON ELECTRONIC THROTTLE ACTUATORS SAVES MILLIONS
That “bargain” actuator might be your most costly mistake. For high-precision gas systems, the true costs lurk in downtime, wasted energy, and recalibration. Let’s crunch the numbers:
UPFRONT VS LIFETIME COSTS
Quality Actuator | $5,000 (life expectancy of at least 10 years) |
VALUE MODEL | $2,500 (To be replaced every 18 months) |
Surprise: The “cheap” alternative ends up costing 2.8X more over 10 years
HIDDEN SAVINGS FACTORS
Energy Saving: Best in class actuators reduce gas waste by 12-18% ($50k/year savings in large plants)
Maintenance Labor: 1 hr/wk debugging x $40,000/yr = +$62,400/10 years
FAILURE COST ANALYSIS
Unscheduled downtime: $15,000/hour in car paint shops
Side products from the poor control of the gas: 3-7% of the production
SMART BUY CHECKLIST:
? 10-year warranty coverage
? ≤0.5% hysteresis specs
? Local service centers
Coming Up: The future of actuator tech — what’s next in 2025 and beyond….
The Next Generation of Electronic Throttle Actuators: Intelligent, Green, and Self-Tuning
The actuators of tomorrow are not just mechanical — they’re predictive, adaptive and ecologically friendly. Here’s what’s on the horizon in next-gen Electronic Throttle Actuator technology:
AI-enabled Predictive Maintenance
Vibration pattern analysis for the advance prediction of bearing characteristic 3 months PRIOR TO THE FAILURE DUE TO WEAR
The gas density dependent response then can be used to optimise the response of an auto-tuning algorithm for gas density.
Green Tech Innovations
Regenerative braking that converts closing power into electricity (invented by Festo)
Hydrogen-ready for the future of fuel
Wireless Revolution
No conduit runs with IO-Link Wireless
Redundant Control in Critical Systems using Mesh Networking
Industry Change: The U.S. Department of Energy predicts 37% market growth for smart actuators by 2027 (energía.gov/industrial-decarbonization).
Your Move Now:
Audit current actuators for legacy “dumb” units
Introduce 1-2 smart pilots/year
Train team members for diagnostic systems