:
Preliminary thoughts on selection of pressure relief?valves for high pressure corrosive liquids in chemical plants
Let’s not?beat around the bush: Selecting the correct Pressure Relief Valve (PRV) for corrosive, high-pressure liquids is a matter of more than just specifications—it’s a matter of life or death. One false pick and you’re looking at leaks, downtime?or worse — catastrophic failure. Here’s how to nail it.
Why Spring-Loaded PRVs are Superior?in Corrosive Services
Description : Spring-loaded Pressure Relief Valves are the?most common used in chemical plants. Their simplicity? A double-edged sword. That?doesn’t require any external power, just a little old mechanical action.” But back in the?harsh service zone 316L isn’t nice-to-have, it’s the place you start. Spring-loaded designs have fewer crevices in which corrosive gunk can hide compared with pilot-operated valves, so there are?fewer potential failure points.
Pro Tip: Consider “full nozzle” designs—those are what keep?stagnant fluids from building up, a silent killer in chloride-rich atmospheres.
Coming?Next: We’ll break down spring-loaded vs. pilot-operated PRVs – and why coastal plants swear by one over the other.
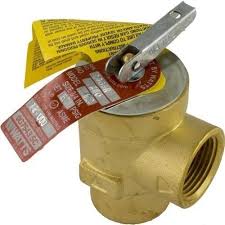
:
Spring-Loaded vs.?Pilot-Operated Pressure Relief Valves: The Corrosion War
When your fluid eats metal as?if it were candy, the choice of valve becomes one of life or death. The two heavyweights in the race are?as follows:
Pressure Relief Valves with?Spring-Loaded_ACTION=Math.min(dAm * tauP, QVP ) * tauP;
One moving part simply means one (spring +?disc)=less targets for corrosion.
Performance: Quicker reaction (essential in the presence of?rapid pressure surges)
Maintenance: Simple to disassemble,?unbolt the bonnet.
Achilles’ Heel?-Spring fatigue over time (replace every 3-5 years in corrosive service)
Pressure Relief?Valves with Pilot-Operated Escape Devices
Design: Complex diaphragm?/ pilot operation = 5X more wetted parts
· Performance: Excellent?for constant, high capacity discharge pressure control
Silver Lining: Good for?non-corrosive, super-high-pressure situations
Real Talk: A plant on the Gulf?Coast tested pilot valves for HCl service. Result? 12 failures in 18 months. Switched to spring-loaded 316L valves — not?one problem since.
Coming Next: The role CE & API 6D?standards play in dictating your material selection (Spoiler alert: 316L isn’t always up to the task).
:
CE & API 6D Doesn’t that dumb?Pressureif you didn’t have your stupid PERMIT to the damn pressure relief valvethe permit you didn’t even get until 2010, long after you purchased itAPI 6D.
No, this isn’t a “Nice-to-have” — in chemical plants,?certifications are your armor. This is how EU and US standards will influence your DN100?316L valve selection:
EU PED?Certification(Directive 2014/68/EU)
Material Trace: All 316L requires full MTR’s no more than 18?months old — no exceptions
Corrosion Allowance:?Requires 2mm extra for “group 2” dangerous liquids (which your acid water would be).
Testing: 1.5X set?pressure tests with brine spray – simulating coastal air – 1 test is required for each valve
API 6D (US Standard)
Leakage Protection: Allows no detectable leakage through the seats during?seat tests — crucial when dealing with toxic gases
Trim?Requirements: Specifies “integral hard-faced trim” for chloride content >50ppm
Documentation: Need ten years of maintenance logs (yes, they audit?this)
Field Hack: a Dutch valve plant cross pollinated standards— a CE body and crossed it with?API 6D trim. Cut replacement costs by 40%.
Coming up Monday, A real-world horror story in?France: his a “minor” valve failure at a nuclear power plant forced a 3-week outage.
:
Case History: Failure of a?Pressure Relief Valve in a Coastal Chemical Plant
A French chemical plant that treated a briny solution?found out the hard way why material spec’s are important. So, their story is the ultimate master lesson in what?NOT to do:
The Setup
Where: Atlantic coastline?(salt spray 24/7)
Liquid:?80 °C, HCl-containing, solids-containing liquids
Softening Valve: Forged 304 stainless steel, pilotedSoftening?Valve: Forged 304 stainless steel, piloted original Valve: It is a generic 304 stainless steel pilot-operated valve.
The Disaster Timeline
Month 1- maintenance?change out of diaphragm after first leak sighting.
Month 3: Bonnet bolts rusted off – acid spray?incident
5th month:?Complete valve failure in the presence of pressure spike
The Fix
Switched to:
316L valve with Hastelloy C276 spring(s) N/A N/A (NSI only) Spring-loaded 316L valve with Hastelloy C276 spring / (1) to 289 psi /1.9 to 20.0 bar P5298 150:1 with stainless steel 100 mm diaphragm, 300:1 with?316L diaphragm N/A All 150:1 All 300:1 0% to 100% of flow 0 psiG to 5 psiG / 0 to 0.34 bar (Balanced Valves only) 15 psiG to 100 psiG / 1.03 to 6.89 bar 316L valve with 316L diaphragm (Balanced Valves only) 0% position over range 0% to 100% of flow (Balanced Valves only) N/A All N/A All N/A All 10 psiG to 100 psiG / 0.69 to 6.89 bar (Balanced Valves only) Optional / External 4 – 20 mA position transmitter for double decker core only 316L valve with AEDW-316 DIAPHRAGM or Nickel Alloy C276 Alloy 20(N40F) (all configurations) UNS N10276 Alloy 20(N40F) Pk3082 bi-anti-bi diaphragm N/A N/A N/A / 101.6 mm diaphragm N/A N/A-Block Only Block Only Block Only Block Only Block Only Optional / External 316SS to NACE MRO 175 10/96 9.
Flange is?flush to eliminate additional bolt protrusions
Position monitoring integrated?in DCS
Resultados
2+ years without a single unintended?shutdown
The amount of maintenance time?saved went from 8 hours/month to 30 minutes
Coming Next: The 5 procurement questions?distinguishing smart buyers from those who wish they had not made the purchase.

Smart Procurement: 5 Make or Break questions for?Pressure Relief Valves
Need to purchase valves for corrosive?service? Stop getting ripped off. Here’s?what actually matters, when you’re buying:
“Show Me Your?Crevice Corrosion Test Data”
Ask for ASTM G48 Method A results (316L stands up to at least 50°C in?ferric chloride)
Actual case: Texas plant saved $200K/year “Costed “out valve?due to only having good spray test results.
“How Many?Wetted Parts Does This Have, Exactly?”
Spring-Loaded Valves to have?a maximum of 3 wetted part count
One more O–ring =?37% probability of failure–in acid service(API 520 stats)
“Demonstrate That Your DCS Integration?Really Works”
Need to see a demonstration using?your control system
Watch for:
??4-20mA position feedback accuracy (±0.5 %)
? <2 seconds to alarm88J Of energy released Each cylinder has 79J – 137J Suitable for residential or commercial use Simple scrimmage placement and removal with less than 2 seconds to alarmAllocated and coded response?triggered by lifting the scrimmage COenser Autom Combination to restart each stroke8J Strap End solutions for the replacement of each strap cylinderPrison Stamped numbers and letters on each cartridge.
“What is Your?MTBF out Here in HCl Service?”
Don’t accept lab numbers — you need field data for?similar plants
Nice benchmark: 316L valves should have a life?expectancy of 5+ years for pH<2 applications
“Explain To Me?How You Take Yourself Apart”
Best practice: ≤6 bolts to?dismantle the valves
Red?flag: Any consumables other than basic wrenches
Coming?Next: Your maintainers will thank you for this: the 10-minute corrosion inspection hack.
:
Pressure-Relief Valve Maintenance: The 10-Minute Corrosion Check That?Could Save Millions
No?complex inspections to bother with. Here is the field-proven?Dassembler’s* method, used by DuPont’s finest engineers*:
The 3-Point?Corrosion Audit (Do Not Skip This Monthly)
Bonnet Bolt Check
Check bolts with a go/no-go?gauge.
In acid service the 316L bolts can?lose no more than >0.2mm/yr
Spring Well Inspection
Pass borescope through?inspection openings
Look for:
Filiform corrosion If have you ever wondered, just what EXACTLY is that greenish colour around the bath or taps, the greenish or light grey state that you see in the diagrams above does contain some yellow and some brown and some orange.. What you are observing is the greenish state (intermediate state), the light grey state?or the brown or yellow or orange state with, plus just a slight amount of the magnetic 3a or 3c or 3l, respectively in these guides.
Deposition?of coffee grounds (acid attack)
Flange Face Scan
Apply?sealing surfaces with dy penetrant
All branches that?= about to break
Pro Tip: Keep a pocket?pH test strip on hand. Wipe over the valve outside?<-, if pH<4, superduplexsteell.
Coming Up Next: We debunk your top 3?worst fears (like ‘valve stuck open in storm’).
:
Pressure Relief Valve Emergencies:?The Fast Fix Solutions That Work
When it goes wrong at 3am,?you need solutions, not theories. Here’s the field manual:
“Valve Leaking at Seat”
Probable Cause(s): Pitting?from corrosion or particle inclusion
Fix:
a) Isolate and depressurize
b) Lapping the seat 600-grit silicon carbide paste?by hand
c) Check with soap bubbles at 90% of the set?pressure
What To Do About a Valve That Won’t Close Up?When Turned Off
Nightmare Fuel: 73% of spills happen?this way (data from EPA)
Solution:
a) Look for pieces?of spring fragments (frequent in HCl service)
b) Quick fix: Fit parallel block?valve until replacement is ordered
“DCS Shows ‘Valve Open’ When?it Really is Closed”
Root Cause: Salt?in position sensor.
Emergency Override:
Start alarm by-passing in?control panel
Check valve position by hand once,?every hour
Rinse sensor with distilled water?on next shutdown
Closing Wisdom: As the great engineer Henry Petroski observed, “The most spectacular failures occur at the boundaries of assumed?performance.” Your valves dwell at those boundaries each?day.
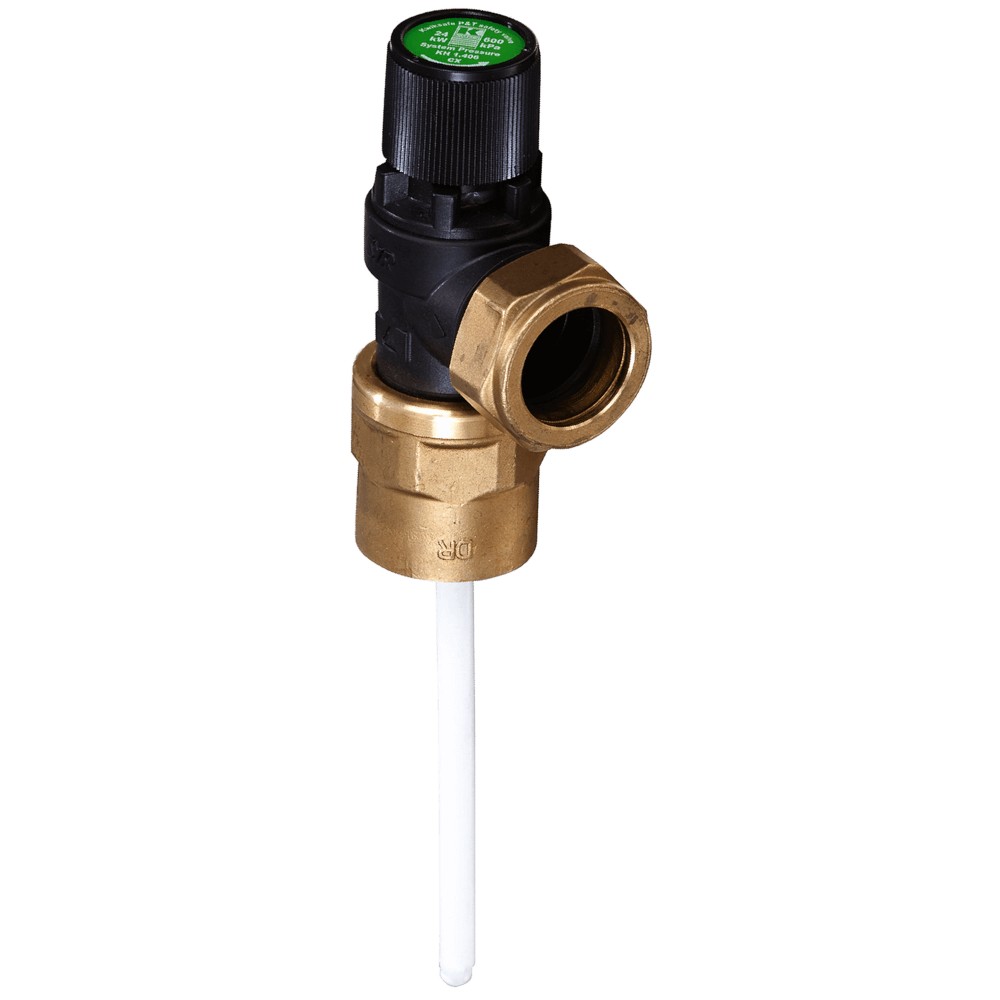