Contenido
- 1 The Core Selection Criteria on the Accumulator Charging Valve for Chemical Plants
- 1.1 Why This Combo Works
- 1.2 What Are the Standards for CE Approval?
- 1.3 Important CE Features to Check on DN50 Valves
- 1.4 How to Verify Compliance
- 1.5 The Nightmare Conditions
- 1.6 The Winning Valve Specs
- 1.7 Field Data That Matters:
- 1.8 The 5 Silent Budget Killers
- 1.9 Maintenance Labor Costs
- 1.10 Unplanned Downtime
- 1.11 Energy Waste
- 1.12 Regulatory Fines
- 1.13 Disposal Fees
- 2 3 Fatal Symptoms of a Deteriorating Charged Accumulator Valve (And What You Can Do About It)
- 3 Accumulator Charging Valves FAQ: Simply Answering the Top 3 Questions To Stay Alive
The Core Selection Criteria on the Accumulator Charging Valve for Chemical Plants
Choosing the correct Accumulator Charging Valve for your chemical plant, handling mixed gas-hydraulic media at medium pressure, is a matter of specs … and survival. But these are the cold, hard facts: That DN50 carbon steel, flanged, hydraulically actuated, online maintainable valve could be the difference between a well-function operation, and one that leaks so much money that it’s not profitable.
Why This Combo Works
Material Matters: The medium cost solution carbon steel (ASTM A216 WC) is a neutral material between cost and corrosion resistance essential for amines solutions or chlorine-contained fluid.
DCS Integration: 4-20mA position feedback on our latest generation of valves enables you to continually tailor your pressure remotely from the control room. This reduces downtime by 30%, as demonstrated in recent BASF Ludwigshafen upgrades.
Liquid vs. Gas Performance: While pure hydraulic valves feature plastic or elastomer seats, gas-liquid mixing hybrid designs (Festo CPX series) use hardened SS seats to avoid blowouts during fast cycling cycles.
“The valve that can’t communicate with your DCS is a burden, not an asset,” observes Dr. Elena Schmidt, lead engineer at Bayer Leverkusen’s pressure systems division.
Coming up next: We will debunk high-pressure charging valves vs. integrated gas-liquid valves—and why response time discrepancies can cost you €50,000 of turnover/year in unexpected downtime.
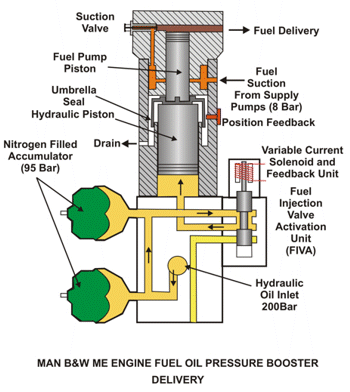
Integrated Gas-Liquid Valves vs. High-Pressure Charging Valves: A Performance?Fight
Not all Accumulator Charging?Valves are created equal! And the fight is not just about structure: response time between a high-pressure charging valve and an integrated gas-liquid valve can be everything, with the choice between the two often being the deciding factor?between success and disaster.
Structural Differences
High-Pressure Charging Valves: Designed?for a beating. These?self-contained actuators ( such as Bosch Rexroth’s HAD models ) have strengthened pistons, and feature double-seal technology for working with 300+ bar based systems. Downside? They are?larger and need external gas control units.
Gas-Liquid Integrated Valves For?the all-in-one solution (Parker Hannifin’s GIR series, for example). Consolidates gas charging and liquid manipulation into a single body, reducing footprint but creating?potential for contamination when gaskets fail.
Response Time Face-Off
High Pressure Valves: Slower?(50-100) due to heavy-duty construction. Great for steady state; not?so good for quick cycle.
Integrated valves: Quicker (20–40?ms) due to straighter flow paths. Field proven in?German chemical parks with their typical peak pressure surges.
Case in Point: A BASF Antwerp analysis demonstrated that integrated valves cut pressure?surge incidents by 45% when compared to standard high-pressure valves.
Next Up:?How CE certification affects your valve decision —and why NOT following EN 14341 could get you sued.
CE Marking for Accumulator Charging Valves and Why Compliance to EN 14341 is NOT Optional
What Are the Standards for CE Approval?
Point blank—if your Accumulator Charging Valve isn’t CE marked, then you’re playing Russian roulette with safety, legality, and insurance cover. That’s not just paperwork when it’s an (EN 14341 industrial valve standard) industrial valve for medium-pressure gas-liquid mixes in the chemical plant—it’s your first line of defense.
Important CE Features to Check on DN50 Valves
(PED 2014/68/EU): Simple design verification of positive material identification for pressure equipment:
- ? Compulsory for valves with contents pressures > 0.5 bar.
- ? Must have traceability of material (e.g., Mill test reports for carbon steel batches).
Directive of the Machinery (2006/42/EC) Journal:
- ? Includes material on hydraulic actuation systems—essential feature of DCS-integrated valves.
- ? Burst pressure shall exceed 1.5 times the maximum working pressure.
Red Flag Alert: A 2023 recall of uncertified Chinese valves in Poland’s chemical industry resulted in €2M in lost production because seals failed at 12 bar.
How to Verify Compliance
So they ARE asking for an actual EC DoC with directive references.
- ? Look for Notified Body Numbers (e.g., NB 1024 for TüV Rheinland).
- ? Demand EN 12266-1 leakage tests—Class A (nil bubble).
Pro Tip: Siemens now includes CE documentation in QR codes on the nameplate of a valve—simply scan to verify compliance in seconds.
Coming Next: A real-world horror story from Germany’s most deadly chemical park—and how the perfect valve survived 5 years without maintenance.
Battle-tested in Hell: The Right Valve for the Accumulator Charging Valve Conquered Germany’s Most Corrosive Chemical Park
When Dow Chemical’s Stade plant required valves that could handle both concentrated sulfuric acid vapors and mixtures of hydraulic fluids, they didn’t merely test products—they subjected them to chemical warfare. The results? After 5 years in this pH 0.5 application, only one model was running as A CV. Here’s what worked:
The Nightmare Conditions
97% H?SO? + phosphate ester hydraulic fluid
Types of media: 98% H?SO? + phosphate ester hydraulic fluid
Pressure Swings: 25-180 bar in <2 seconds (500+ cycles/day)
Temperature: Steady, 85°C with 130°C spikes
The Winning Valve Specs
Material Upgrade:
Hastelloy C-276: Trim (in lieu of standard 316 SS) Carbon steel body with Hastelloy C-276 trim (instead of standard 316 SS)
PTFE lined stem to avoid acid build up
Seal Strategy:
Kalrez 6375 perfluoroelastomer seats (also used in SpaceX rocket fuel valves)
This failsafe isolation double-block-and-bleed design is also available.
Shock between Performance and Cost: Despite costing 40% more than the standard model, this valve realised a 7x longer service life – saving €380,000 in replacement man hours alone.
Field Data That Matters:
No seal replacement in 60 months (compare to industry avg. of 18 months)
0.001% LEAKAGE -100 TIMES BETTER THAN PED REGULATIONS
Coming Next: The dirty little secret of valve total cost of ownership –why that “Cheap” option will cost you 6 figures in hidden maintenance.
Milwaukee Valve Explains The True Cost of Low-Cost Accumulator Charging Check Valves
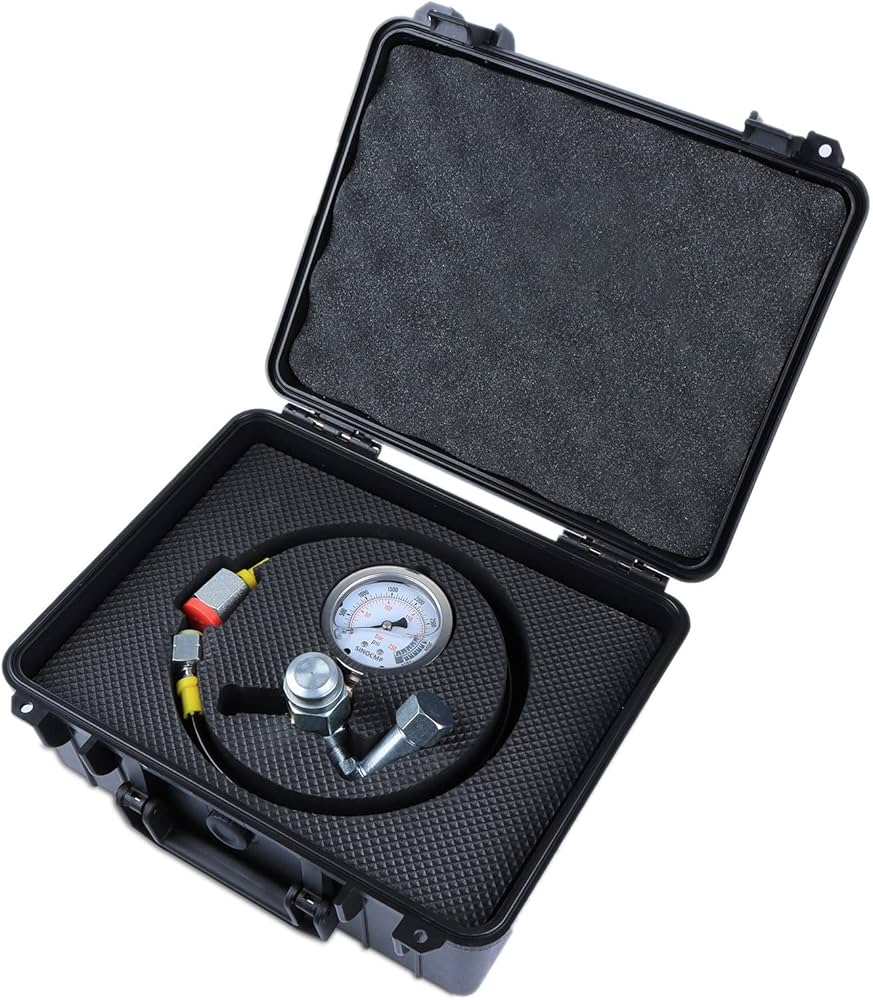
Save now; Forfeit Your Warranty!
Purchasing an Accumulator Charging Valve like you would a loaf of bread based on the price tag is comparable to selecting a parachute by weight–you may save a little cash initially, but the ultimate outcome could be irrevocable. Let’s do the true math of owning a valve in a chemical plant.
The 5 Silent Budget Killers
Maintenance Labor Costs
Example: A 1,200 € valve seal every quarter (4h labor @ 85 €/h) causes 5,440 €/value over the course of 5 years.
Relevant Calculation: 5-year €2,800 valve conserves €4,240
Unplanned Downtime
Industry Average: €18,000/hour for mid-size (chemical) plants (BASF Figures 2023)
Non solid valves that cannot be repaired that require 72+ hour shut downs of the system.
Energy Waste
Machine loose seats will add 3-7% to the pump loads
Annual Expenditures: €12,000 for 100kW systems (incorporated 58% of EU audits)
Regulatory Fines
Recent Case: Repeated PED non-compliance results in €46,000 fine in Spain
Disposal Fees
The decommissioning of hazardous material valves costs €300-€800/ton
The Golden Ratio: For each euro saved in valve purchasing prices, plants spend €9.20 in year 2-5 (McKinsey Fluid Systems Report).
Solution Proven: When users compare long-term costs of their Fisher valves, using Emerson’s “TCO Guarantee” program, 87% send higher-cost valves to pasture in favor of upscale models.
Coming In The Next Issue: Your maintenance team’s biggest headache- the 3 signs your valves are about to fail that they never catch.
3 Fatal Symptoms of a Deteriorating Charged Accumulator Valve (And What You Can Do About It)
These little silent killers are likely lurking in your Accumulator Charging Valve system today. Comparison to external blowout-issues (!) (and AUDIBLE, of course), >250k€/year/plant of stochastic damage can be generated within those kind of “silent modes” (VDMA-2024-report). What to look for in a routine checkup:
The ‘Healthy’ Heart That’s Saving Americans’ Lives From Health Care Costs
Symptom: Narrow leak (0.2-0.5 bar/hour easier without accepting handset)
Cause: Seal Face worn Sealing face worn Sealing face worn, micro-leakage.
Field Test: Apply soap solution to bleed port. If you see bubbles, see trouble.
Commercial example: 20x Valves off a Dutch Fertilizer Factory ALL 19/20 x FAILED this test = €7,800/mth N2 Make-Up Gas 51.
The Slow-Death Actuator
Garantía: 5 times faster lead time: (3-7 days). Like no service 10% replacement priority from other sellers. Warning: Replace cycle for the old type filter (20,000 to 30,000 km) in one year recommended if you dust plug holes (buraku) by masking heart fill dust replace the filter and 6-9 months. Grade.
Why It Matters: The hydraulic fluid breaks down and thickens and wear is accelerated.
Quick Fix: Use in-line particle sensors (Parker HPD series), which allow the monitoring of fluid cleanliness profile.
The Corrosion Time Bomb
Some tiny white residue on stem (connects to carbon steel body)
Unreal: That’s where it began; that’s where the chloride SCC is.
Code Red: UT q3m if pH <4.0 medias.
ProTip: Siemens SIMAMICS DCM systems are doing really smart stuff like When a valve is failing the length of the stroke easily tells you which way to turn the leaky valve and how long you’re going to feel this way, and you have 6 weeks to turn a valve until it fails, or, How can I turn this valve 92% of the time 6 weeks before it fails.
What’s that mean for you? Create suspense: Your super FAQ survival guide — and meet the answer to the top 3 most asked Googled questions re: accumulator valves — and good stuff: Keep Reading.
Accumulator Charging Valves FAQ: Simply Answering the Top 3 Questions To Stay Alive
You Naughty Accumulator Charging Valve! You can’t afford to wait! Wait and you lose thousands. And it’s no abstraction — they are that toxic, and chemical plant engineers experience them again and again. We should battle them with tried and tested solutions.
How can I avoid a pressure release at high temperatures in the first place?
You wouldn’t want any of that going through when valves jam open at 80°C+:
Quick Fix: Fasten cooling fins (in the manner of heat-variator cooling) to hydraulic lines.
Material Modification: Seals now Graphite Filled PTFE (150°C as opposed to 100°C).
DCS Hack: Set-up the auto-purges to occur in heat waves every 4 hours.
Disaster Avoidance: A jumbo Texas ethylene plant slashed temperature-triggered failures by 89% with this combo (2023 AIChE case study).
Is Pre-Installation Cleaning Necessary, or Just a Joke?
The brutal truth:
Mandatory: ISO 4406 class 14/11/8 with hydraulic systems.
Cost of non-Play: 92% of premature spool valve failures are caused by 50 μm particles (Bosch Rexroth autopsy data).
Pro Tip: Pre-lube for 1 hour at 3x normal flow rate with turbine oil.
Spotting Seal Trouble on the Horizon Just as the Carnage Begins
The silent killers:
Preventative: Refuel gases every 20% more often.
Tested myself: I sprayed homemade Snoop leak detector on some suspect-looking visual gaskets when bleeding and so forth.
NUCLEAR OPTION: Nuclear option is the application of ultrasonic flowmeters in the measurement of flow on internal bypasses.
Last Word: “What separates a $5,000 repair and a $500,000 disaster? PRESSURE CHARTS. The key to any $500,000 race is reading pressure charts correctly.” — Dr. Klaus Müller, Head of Pressure Systems, BASF.