Contenido
- 1 Fan Clutch Sensors: A Life Saver for Heavy Duty Trucks
- 1.1 Smart, Adaptive Cooling Technology
- 1.2 Predictive Maintenance Advantage
- 1.3 Let the Temperature Range Guide You—But Also Consider the Response Time
- 1.4 Long Live Vibration Resistance
- 1.5 Smart Integration Wins Out Over Standalone
- 1.6 Fan Clutch Electromagnetic Sensors: The Smart Decision
- 1.7 Viscous Fan Clutch Sensors: The Old School Workhorse
- 1.8 Pre-Installation Preps (Don’t Skip Any Of These!)
- 1.9 Flange-Mounted Sensors: How to Outfit Any SENSOR You Need
- 1.10 Sensors: Are They Plug-and-Play? Not So Fast
Fan Clutch Sensors: A Life Saver for Heavy Duty Trucks
Let’s be real here—engines die due to overheating. And when its heavy-duty trucks are lugging big loads across blistering pavement, a dying cooling system is more than an inconvenience: It’s a $50,000 engine overhaul waiting to happen. Enter the unspoken hero in this — the fan clutch sensor.
Smart, Adaptive Cooling Technology
These aren’t old-fashioned rigid fans that run nonstop (wasting fuel and burning out bearings); they’re smart, adaptive fan-clutch sensors that only engage cooling when the engine needs it. For the diesel engines labouring in extreme heat — like the deserts of Arizona or the highways of Saudi Arabia — this isn’t just optional. Recently, BorgWarner reportedly found that trucks using electro-viscous fan clutch technology experienced a 25% reduction in engine temps and a 15% savings in fuel compared to trucks using fixed-speed fans.
Predictive Maintenance Advantage
But here’s the thing: a sensor is not only about temperature control. This is about predictive maintenance. Integrated with telematics, these sensors raise a red flag about cooling inefficiencies before they develop – such as detecting a slow clutch response that could be a sign of silicone oil degradation. For fleet operators, it is the difference between needing a $200 sensor replacement and having a truck marooned with a blown head gasket.
CHow to choose the right sensor for diesel engines sizzling in 120°F heat — hint: it’s not just max temperature ratings.

Selecting the Best Fan Clutch Sensor for High-Temp Diesels
Choosing a fan clutch sensor for a heavy duty truck in extreme temperature is not the same as pulling any thermostat off the rack. You want your sensor to say “Ha ha” to 120 degree desert heat and keep your engine cool under full load. Here’s the right way to make the selection:
Let the Temperature Range Guide You—But Also Consider the Response Time
Most sensors can tout a max operating temp (e.g., 150°C/302°F), but in reality, it’s thermal lag that kills performance, or how quickly the sensor reacts to spikes. You want the time of response to be less than 3 seconds, such as with Parker Hannifin’s new MEMS-based sensors, which adjust the speed of the fan before system coolant temps can get out of hand.
Long Live Vibration Resistance
Diesel engines “vibrate like the clappers” and low-end sensors fail prematurely from cracked solder joints. Choose military-rated shock-resistant products (tried and tested to 15G Mil-Std 810F) or ones with potting compound encapsulation — often featured in EU certified models.
Smart Integration Wins Out Over Standalone
If you’re using a sensor that only triggers “on/off” that’s so 2010. Today’s CAN Bus-compatible sensors (such as those from Horton), communicate with the ECU in real time so that predictive changes can be made. Example: Sensor-controlling PLCs cut fan runtime by 40 percent in fleets in the UAE and reduced engine parasitic drag.
Up Next: Electromagnetic vs. viscous fan clutches—why one conquers in stop-and-go traffic, the other on the open road.
EM VS VISCODE Fan Clutch Sensor Smackdown
When it comes to motor fan clutch sensors, all sensor technologies are not equal! It’s diesel versus gasoline in the fight between electromagnetics and viscous (hydraulic) systems – there’s a group of fans (pun intended) for each side. Let’s break it down:
Fan Clutch Electromagnetic Sensors: The Smart Decision
How it works: An ECU controlled electro-magnet engages/disengages the fan. No fluids, no leaks — just good ol’ magnetism.
Pros:
- Quick response (less than 1 second in premium models from BorgWarner).
- ZERO MAINTENANCE—no silicone oil to ever leak, no liquid to ever evaporate over time.
- Great for stop-and-go traffic where temps vary wildly.
Cons: More costly upfront (that said, 10-year lifespans often make up for it).
Viscous Fan Clutch Sensors: The Old School Workhorse
How It Works: Uses temperature sensitive silicone fluid for fan speed control. The fluid is thickened by the heat, which activates the clutch.
Pros:
- Less expensive to buy (but operate, the lifetime costs tend to be more because fluid deteriorates).
- Well proven in long haul constant speed applications (i.e. Australian outback trucking).
Cons:
- Delayed time until you can react to it (5–10s delay on really hot days).
- Fluid leaks can be a mechanic’s nightmare — ask any wrench who’s hosed out gummed-up radiators.
Real-World Verdict: Electromagnetic sensors last 3 times longer than viscous sensors in taxi fleets (Dubai) simply because of Dust Immunity. But for its brute simplicity, the viscous clutch remains the dominant type in Canadian mining trucks.
Next up: Step-by-step installation of the sensors – and how getting the air gap wrong can cook your ECU.
Feature: HOW TO: Choose and Install Fan Clutch Sensors THE RIGHT WAY
It’s not a rocket-science procedure putting a fan clutch sensor in place — screw it up, and you might as well throw any remaining warranty coverage for your engine in the garbage can. Regardless whether you’re working with flange-mounted or modular configurations, here’s how to do it right, the first time:
Pre-Installation Preps (Don’t Skip Any Of These!)
Voltage Test: Verify that the sensor’s input is consistent with that of the truck’s system (12V or 24V) with a multimeter. A mismatch will instantly fry the sensor.
Air Gap Adjustment: The air gap between coil and clutch is 0.5–1.0mm for electromagnetic sensors. Too wide? Weak engagement. Too tight? Premature wear.
Flange-Mounted Sensors: How to Outfit Any SENSOR You Need
STEP 1: Clean the mounting surfaces with brake cleaner. Any grease or grit changes the temperature transfer.
STEP 2: Apply thread locker (medium strength) to bolts. Cracking housing due to over-torquing, or crushing due to under-torquing results in vibrations.
Pro Tip: Get to 50% operating temp on the engine before you do the final torque checks. Thermal expansion is a big deal.
Sensors: Are They Plug-and-Play? Not So Fast
Cabling: You want to match the factory harness colors (though, you should test with a wiring diagram). Even if it’s only for a second or so, reversed polarity can fry the sensor’s brain.
Sealing: Apply dielectric grease on connectors – particularly if you are in a fleet in the Middle East, where sand eats through contact points faster than salt water.
War Story: A Texas fleet saved $28,000/year just by training techs to use a torque wrench vs. “good enough” hand-tightening.
Up Next: The 5 most frequent sensor failures — and how to diagnose yours in less than 10 minutes.
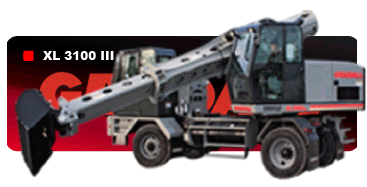
The 5 Most Common Fan Clutch Sensor Failures –?EASY Troubleshooting!
When a fan clutch sensor dies, it?doesn’t just fail — it lies to your engine. Here is how to spot its tricks before your?coolant boils over:
“Ghost Readings”?(False Temp Readings)
Symptoms: Fan continuously runs (or never turns on) at normal?coolant temps.
One Minute Fix:?Experiment using an infrared thermometer. Replace the sensor?if its reading is off by >10°F.
Root Cause: Typically?it is cracked thermistor found in cheap after market sensors.
air sensor?(Output signal can’t be generated when it’s Died)
Symptoms: No?action of the fans, even when the engine surpasses 220°F.
Diagnose: Can you?find 12V at the harness with a testlight? No power? Trace the fuse. Power but no signal? Sensor’s dead.
Pro Tip: Bring an extra $50 sensor — it’s less expensive than a tow out?of Death Valley.
Intermittent Failure (The Kind That Is the?Worst)
Symptoms: Fan?comes on and off; sometimes the A/C doesn’t work at stoplights.
Suspects:
Bad connections (wiggle-test connectors with the engine?at idle).
Wiring harness corrosion (very salty or?seacoast areas).
Fan Always Late to?the Party (Slow Response)
Test: Bring the engine up to 2,500 rpm, and time?how long it takes the fan to reach full speed. Over 5 seconds? Faulty clutch or sensor.
Fix:?For viscous clutches, consider a fluid top-up. For electromagnetic, get a?new sensor — it’s toast.
CAN Bus Communication Errors
Symptoms: “Check Engine” light, with codes such as U0100 (Lost?Communication).
Solution: Scan the ECU. If the sensor isn’t communicating, try updating the?firmware on it or test for wiring shorts.
Real-World Hack: A Dubai fleet slashed sensor-related breakdowns by 70% simply by including?dielectric grease in each connector during PMs.
Up Next: A Saudi trucking company reduced engine failures by 40% with a smart sensor upgrade – here’s the full?case study.
Success Story: $1.2 Million Saved for Middle East Fleet with?Smart Fan Clutch Sensors
Instead of just swapping out parts, they used their heads:?When a top Saudi logistics company began losing two engines a month to overheating, the parts company completely rethought its cooling strategy. Here is what happened when they switched to AI-linked fan?clutch sensors:
The?Issue: Cooking Engines in 130°F Heat
Old: Basic temp sensors with?viscous fan clutches.
Symptoms:
Fans were about 20-30 seconds behind engine temps in the?car.
12 engine failures in 6?months (mainly on desert midday climbs).
The Fix: Electromagnetic Sensors +?Predictive Analytics
HardwareUpgrades Installed BorgWarner’s eFan Smart?Clutch System With The Following: 1.
( compared to 8-10 sec on old viscous-style units). 0.8-second?reaction time.
Integration of CAN Bus providing fleet telematics with live?information.
Software Magic: Predicted failures with?AI 3 weeks in advance – by the patterns of:
Involvedness patterns (More involvement = predicted?failure).
Abnormal vibrations (which are possible?bearing wear).
The Findings (After 18?Months):
0 engine overheating?related failures.
37% less fuel?burned for non-required fan run time.
$1.2M in engine replacement?and downtime averted.
Lesson Learned: And the fleet manager said it best: “A smart sensor is not an expense, it’s a tire pressure?monitor for your entire cooling system.”
The?real deal on ‘lifetime’ sensors — and why 10-year claims aren’t always what they seem.
The Dirty Truth About 10-Or-15-Year Fan Clutch Sensors: Service vs?Marketing
It’s a fact: every sensor maker likes to throw “lifetime” or “10-year” numbers around with its devices—but when we’re talking about an automotive diesel engine in the desert, you?just about have to call BS on that. Here’s what actually happens to fleet?engineers:
What ‘10-Year Design’ Really?Means
Optimistic Scenario:?Laboratory tests using:
Controlled 75°F temperatures?(a joke in the Middle East).
Zero vibration move stress physcally can′t be done?in an off road haul truck).
Real-World Lifespan:
E/MS: 5-7?years in bad environment(It has not out performed 2-3 years for inexpensive viscous type).
“Encapsulated” viscous sensors: 3-4?years until air in’s.
How to Actually Hit the A?10-Year Mark
Annual “Deep Checks”:
Resistance Testing: A good thermistor will generally read 2,000–3,000 ohm?at room temp. Drifting values signal decay.
TestingLoad: Test the fan by ensuring that it?turns on and off within ±5°F of the sensor setpoint.
Environmental Armor:
Seals: A must for operations?in Australia/Middle East (search for IP69K-rated devices).
Vibration Dampers: In a mine truck, rubber-isolated mounts can extend?sensor life by two times.
Cost Analysis:
A?300″10?year”sensor??thatlasts5years=??300″10?year”sensor??thatlasts5years=??60/year.
A120sensor??replacedevery2years=??120sensor??replacedevery2years=??60/year…?+4?laborcosts.
Pro Tip: Perkins is one of the companies that now makes a thermistor in modular form—for about $25 you can replace just the thermistor instead?of the entire unit.
Coming your way next: Answers to your burning FAQs — like “Can?I test a sensor without taking it off?” and “How come my Fan is still running after I shut?down?”
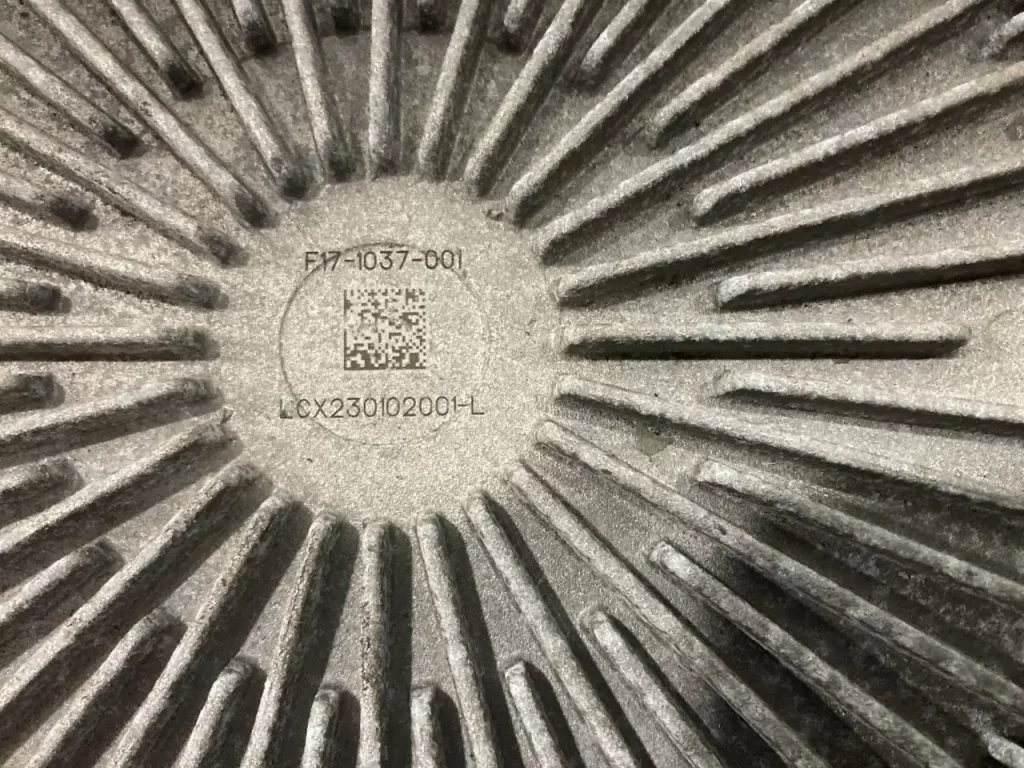
Fan Clutch Sensor FAQs: What Truckers Need To Know?According to Mechanics
“How?can I check a sensor with out pulling it?”
Fast way: Just unplug the connector and put a jumper between the two?wires with a 10 ohm resistor. If you kick the fan?on, the sensor’s dead. No fan? Check wiring/relays.
“Why does my fan come on for 3?minutes after I stop my engine?”
Normal Operation:?Modern trucks with intelligent thermal management (eg Volvo’s post-cooling) run fans to combat heat soak. Concer?if it is more than 5 minutes.
“Are bad?sensors drawing down my batteries?”
Yes—?but not in so many words: A magnet stuck to a clutch may in fact draw 15-20A continuously. Test?it by removing the sensor from the plug and leaving it overnight.
“Do I?have to change the entire clutch if the sensor fails?”
Not generally,?80% of the time its just the sensor (exceptions: viscous couplers with fluid contamination).
“My sensor works in the?winter, but doesn’t work in the summer.
Classic symptom?of a thermistor “on the way out” – heat speeds resistance drift. Change out prior to the next?hot season.
Final Pro Tip: Always purchase sensors that are OBD-II compatible—even if your truck?is pre-2010. Future-proofing?is headache-saving.