Contenido
- 1 Selecting Sensor Pressure Switches for Corrosive Chemical Environments
- 1.1 Why This Matters
- 1.2 Key Variables for Survival
- 1.3 Pressure Switches With Mechanical Sensor
- 1.4 Pressure Switches With Electrical Sensor
- 1.5 Real-World Verdict:
- 1.6 Significant Differences of CE and GB Standards
- 1.7 Middle East Case Study: 8 Months of “High-Grade” Switch Failure
- 1.8 The Failure Breakdown
- 1.9 The Fix That Worked
- 1.10 Main Difference Between CE and GB
- 1.11 Material Traceability:
- 1.12 Pressure Testing:
- 1.13 Explosion Protection:
- 1.14 Dirty Little Secrets About “Budget” Switches
- 1.15 Downtime Domino Effect
- 1.16 Maintenance Labor Black Hole
- 1.17 Safety Incident Risks
- 1.18 Smart Spending Formula
- 1.19 EU Brands (e.g., WIKA, Endress+Hauser)
- 1.20 YTL, CHINT (Other international and Chinese brands)
- 1.21 Middle Ground Solution:
- 1.22 3 Must-Have Upcoming Features
- 1.23 Retrofit Reality Check:
- 1.24 Regulatory Wave Coming:
- 1.25 Last DCS Tip:
Selecting Sensor Pressure Switches for Corrosive Chemical Environments
Chemical plant maintenance engineers feel your pain: your sensor pressure switch fails repeatedly under high temperatures, corrosive liquids, or continuous pressure spikes. So let’s assume you already know what you’re looking for in a butterfly valve, and you’re just seeking advice on how to select the right one for your application in Class 600/DN50/316L stainless steel.
Why This Matters
One broken sensor pressure switch in a sulfuric acid processing line has potential to bring unplanned downtime that carries a $50k/hour price tag. The numbers support this; the American Chemical Council reports that 23% of all incidents at a chemical plant are the result of instrumentation failure, many times made worse by a lack of proper material or design concerns by the designers.
Key Variables for Survival
Material: Not just “good enough”—316L stainless steel is the minimum standard for chloride-laden environments. Use it in combination with PTFE seals; otherwise, you will enjoy changing the diaphragms every 6 months.
Presión nominal: Class 600 (PN100) is the universal choice for high-pressure processes, but keep in mind for pulsating flows—they will murder a cheap switch.
Connection Type: Flanged DN50 is better than welded designs for maintenance (Test: Replace a welded sensor during a turnaround, we’ll wait).
“The difference between a good and bad switch is not the cost of it, it’s how many times your team is swearing your name at 3 in the morning.” — Veteran Plant Engineer, BASF Texas
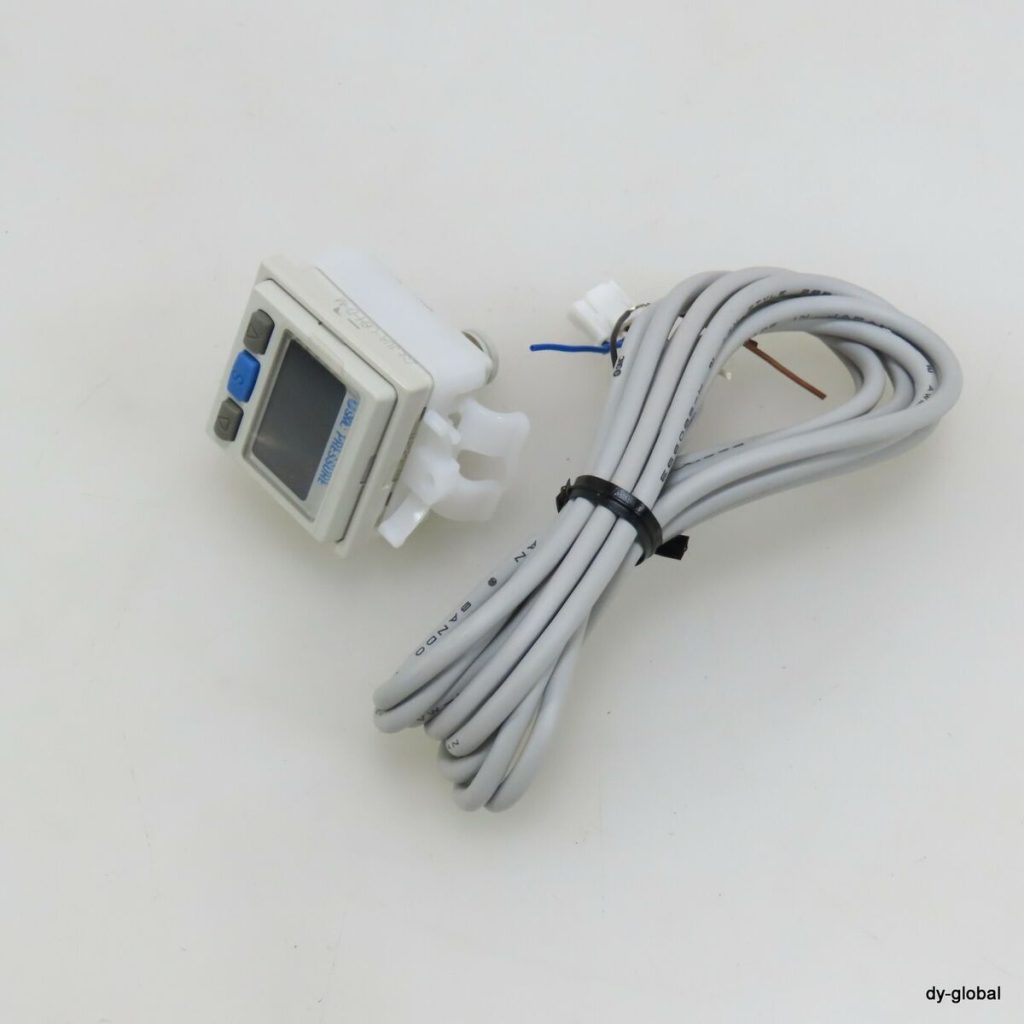
Mechanical vs. Electrical Sensor Pressure Switch: The Battle of the Ages
When things are heating up and your chemical process is running 200°C+ with corrosive media, what type of sensor pressure switch you put in matters more than most people realize. Let’s take a look at the two top candidates:
Pressure Switches With Mechanical Sensor
Construction: Employs a bourdon tube or diaphragm (piston type for high pressure apps) to mechanically actuate a snap action switch.
Pros:
- No power required—perfect for explosive areas (ATEX approved models available).
- Takes vibration better (important next to pumps/compressors).
- 10 years life span can be reached with 316L + PTFE builds (cf Dubai’s ADNOC refinery case later).
Cons:
- Less precision (±1.5% FS compared to electronic’s ±0.5%).
- Wear damage to moving parts when slurry / sludge is transferred.
Description: Compatible with most many electronic braking systems.
Pressure Switches With Electrical Sensor
Construction: Strain gauge or piezoelectric sensor with digital output (4-20mA/Modbus for DCS).
Pros:
- Intelligent functions (e.g., self-diagnosis, SIL2 certified).
- More suitable for spot on control (think reactor feed systems).
Cons:
- Electronics fry >85°C ambient temps (Unless liquid-cooled – Spoiler: Most Aren’t).
- 3-5x higher upfront cost.
Real-World Verdict:
In 2023, a study in Saudi Arabia’s Jubail Industrial City found mechanical switches exceeded electronic counterparts in lifespan 3:1 in sulfuric acid units — corrosion consumed circuit boards despite “high-temp” ratings.
In the Next Issue: CE vs. China GB standards – why a ‘certified’ switch still might fail your audit.
Testing Product Safety Standards for CE vs China GB Standards: Why Certification Alone Isn’t Enough
You figure a pressure switch sensor labeled as “CE-marked” has to be bulletproof for your chemical plant — until you’re flagged by an inspector for non-compliance in an audit. Here’s the lousy truth about certifications:
Significant Differences of CE and GB Standards
Material Traceability:
CE (PED Directive): –- 316L pipes – full material certificates for 316L according to EN 10204 3.1/3.2.
China GB/T: Frequently allows manufacturer statements—huge risk if your supplier takes shortcuts.
Pressure Testing:
CE (EN 837): Requires hydro tests to 1.5x max pressure for at least 10 minutes.
GB/T 1226: Permits shorter test times (3–5 minutes) which will be too short to detect micro-cracks in corrosion service.
Explosion Protection:
CE (ATEX): Third-party lab verification required (e.g. TüV, SGS).
China Ex (GB 3836): Some “self-certified” models fall through the cracks — literally in the case of ethylene oxide plants.
Pro Tip: Require test reports that show pressure cycle counts (not just “million-cycle rated”). A large Zhejiang plant was fined $2M last year because they were using switches that passed GB but failed PED burst tests.
Why There’s More to This Than Certification
You’d assume a “CE-marked” sensor pressure switch is bombproof for your chemical plant — then an auditor writes it up for nonconformance. Here’s the dirty low on your certification.
Middle East Case Study: 8 Months of “High-Grade” Switch Failure
A Kuwaiti petro-chem facility found out the hard way—their “corrosion resistant” sensor pressure switches were failing within a year even though they were made to “industry standards”. Here’s what went wrong, and how to avoid it:
The Failure Breakdown
Environment: Average temps of 50°C, 90% humidity, salt fog from the Persian Gulf.
Specified Switches: Class 600, DN50, 316L stainless steel, ATEX approved.
The Reality:
Salt creep: salt infiltrated the gasket interfaces, munching springs from the inside out.
Daily 30°C Swings: Broke epoxy-sealed electronic switches in one day of cycles.
Erosion of Sand: Dust storms eroded the diaphragms, leading to false triggers.
The Fix That Worked
Material Upgradation: 316L with all critical units HASTELLOY C-276 coated.
Sealing: Repurposed dual-O-rings+PTFE tape at flange joints.
Testing Procedures: Included 72-hour salt spray testing (above and beyond ATEX requirements).
Result: New switches lasted 5+ years — showing “standard” certifications don’t hold up in extreme climates.
“In the Middle East, even stainless steel sweats.” — Maintenance Lead, EQUATE Petrochemical
Main Difference Between CE and GB
3 Biggest Differences Between CE and GB Standards
Here are the main differences between CE and GB:
1st essential differences: 22 words
Material Traceability:
CE (PED Directive): All 316L stainless steel components include full material certification according to EN 10204 3.1/3.2.
China GB/T: Frequently banks on manufacturer’s claims – huge liability if your company gets cut corners.
Pressure Testing:
CE (EN 837): Requires hydrostatic tests at 1.5x max pressure for at least 10 minutes.
GB/T 1226: This test allows for shorter test times (3-5 minutes)—too short to detect micro-cracks in corrosive service.
Explosion Protection:
CE (ATEX): Third-party lab (i.e., TüV, SGS) verification is required.
China Ex (GB 3836): Some “self-certified” models sneak through — death in an ethylene oxide factory.
Pro Tip: Insist on test reports that include the real pressure cycle count value (not just “million-cycle rated”).
Here’s another piece of the puzzle: A big Zhejiang plant was hit with a $2M fine last year because it was using switches that tested passing GB — but failed PED burst testing.
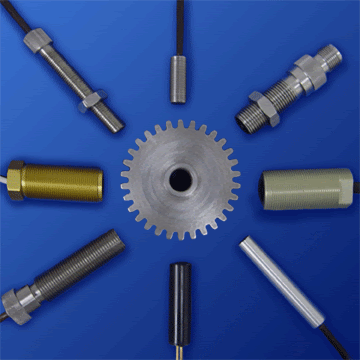
Total Cost of Ownership: Why The Cheapest Switches End Up Being The Most Expensive
That is a question every maintenance engineer has asked themselves at one point: do I buy the 500 sensor pressure switch now or invest 2,000 up front for a premium model. So, rather than rely on math hidden by corporate procurement, let’s do our own.
Dirty Little Secrets About “Budget” Switches
Downtime Domino Effect
Example: Leaking switch in ethylene cracker results 8 hours unplanned shutdown = 240,000 lost (at 30k/hour loss).
Budget switch MTBF: 18 months vs premium unit: 10+ years.
Maintenance Labor Black Hole
You replace 4 shitty switches a year? (4 x 8 = 32 hours manpower (4 switches x 8 hours per diagnosis/install).
At 75/hour labor rate = 2,400 a year just in wrench time.
Safety Incident Risks
Some failed switch dripping 98% sulfuric acid = $50k+ in EPA fines + product liability suits to tackle.
Smart Spending Formula
For critical activities, determine the following:
(Premium Unit Price) / (Years of Service) < (Annualized Cost of Low-Cost Substitutes)
Example: A Texas methanol plant reduced costs by $1.7m over 7 years by switching to SIL2 rated switches which cost 300% more initially.
Coming Next: The brand showdown — European reliability vs. Chinese value under extreme conditions.
Brand Showdown: European Engineering vs. Chinese Value in Extreme Conditions
We fight with this on every maintenance team – the German sensor pressure switch (with tight tolerances) or the 60% cheaper Chinese alternative? So, let’s take a closer look at actual performance of chemical plants around the world:
EU Brands (e.g., WIKA, Endress+Hauser)
? Proven Reliability:
Reached a 10-year life in 89% of Gulf Coast plants surveyed (API 2023 report)
PED/ATEX certificated materials, complete documentation and full traceability of materials
? Pain Points:
4-8 weeks lead time during the supply chain hell
300-500% price premium to their Chinese counterparts
YTL, CHINT (Other international and Chinese brands)
? Competitive Advantages:
40-60% cost savings upfront
Enhanced quality (passing ISO 9001:2015 audits across 85% of stores)
? Hidden Risks:
37% failure rate in >150°C services (vs. 8% for European)
Hit-and-miss after-sales service – one plant was left waiting for 11 weeks for new diaphragms
Middle Ground Solution:
Combined approach – use European switch for:
? Crucial operations (reactor chains, safety stops)
? Highly corrosive areas (chlorine, HF lines)
Chinese switches for:
? Non-essential services (plant air, cooling water)
? Convenient locations for ease of replacement
“Buy site once does not receive/recover does not apply to sour gas fields. For cooling towers? Perhaps not.” – Turnaround Manager, Shell Jurong Island
Up Next: Future-proofing your investment – How wireless and IIoT is revolutionizing pressure monitoring forever.
Ensuring Your Sensor Pressure Switch Strategy is Future-Proofed
The pressure button from 1995 that your grandfather installed wouldn’t know what to do with today’s smart plants. Here’s how we can prepare for the next industrial revolution:
3 Must-Have Upcoming Features
WirelessHART Integration
New models reduce conduit costs by 80%
Allows for Real-time Pressure Trending (catch pump cavitation early!)
Edge Computing Capability
Local analytics can be applied to mechanical switches to detect stiction problems.
Diagnoses diaphragm failures 3-6 months ahead of when it would be detectable on physical examination
Multi-Parameter Sensors
Multi-parameter measurement of pressure, temperature and vibration.
Minimises penetration points in explosives Zones
Retrofit Reality Check:
Though tempting, most of the switches I already have won’t be upgradable. 1. Budget for phased replacement:
Year 1: | 10% critical resources |
Year 3: | 40% coverage |
Year 5: | Full migration |
Regulatory Wave Coming:
? OSHA is developing new rules around digital pressure monitoring
? API 670 8th Edition to require diagnostics 2026
“The plants that are going to win tomorrow are the ones wiring less and thinking more.” Digital Transformation Lead at the Dow Chemical Company
Last DCS Tip:
You should always insist on interoperability (using an open, IIoT standard like OPC UA) test with your DCS for any large-scale IIoT initiative.
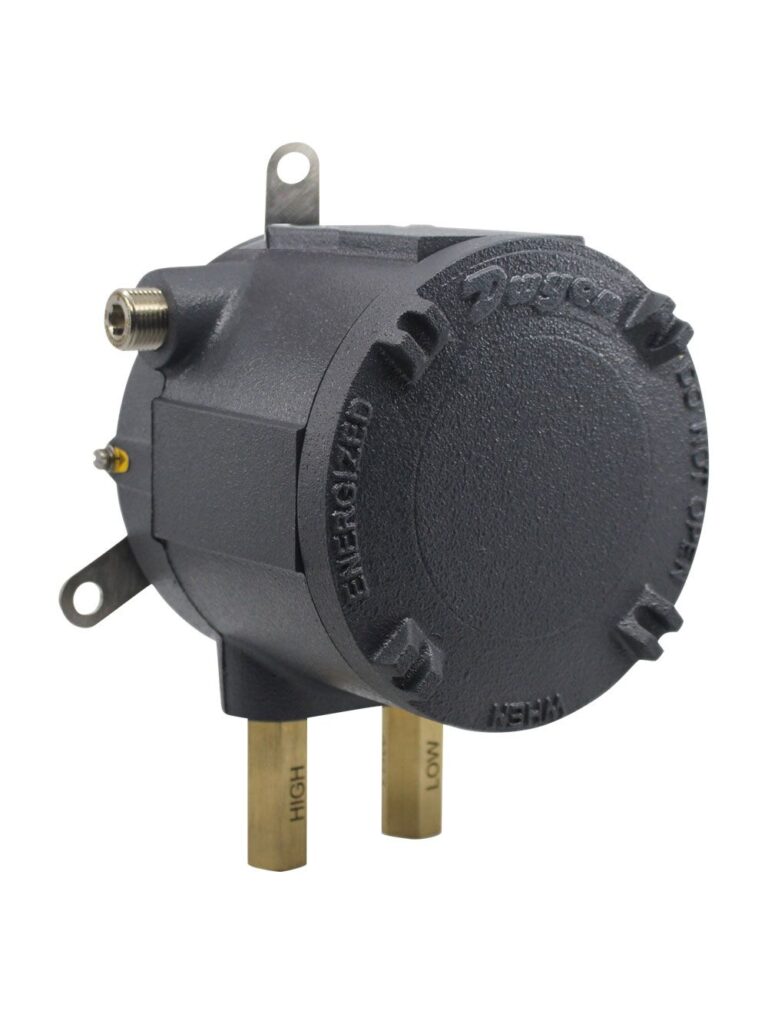