Optimizing Your Reachstacker Fleet in Container Terminal Operations In the challenging environment of?container terminal operations, your reachstacker fleet efficiency can dictate productivity levels. As a maintenance?engineer you’re always fighting against adverse conditions—high dust, salty humidity and continuous operational cycles. The trick to overcoming this battle is with the varying reachstacker parts,?but that’s not easy, how do you even know where to start?
Let’s get to the core?of the issue: hydraulic systems. While Bosch Rexroth and Parker are major players in the market, the designs?are wildly different. Rexroth’s axial piston pumps, for example, are 10% more energy-saving than standard gear pumps, and that’s?essential for China’s emission-reduction goal. Parker’s compact valves, on the other hand, are designed?for space-constrained retrofits. But here’s the rub:?parts certified by a European Conformité Européenne, or CE, use nickel-plated seals for corrosion resistance, while Chinese suppliers such as Hengli prefer cost-efficient rubber composites. What does better in Ningbo’s monsoon?season? The answer may?surprise you.
The Critical Role of Cabin Control Modules in Industrial Operations
The stakes are highest with cabin control modules. A single glitch can bring operations to a halt, costing thousands a minute. Siemens’ modules, compliant with Euro-6, have MIL-STD-810G military-grade shock-resistant equipment—ideal for China’s uneven yard surfaces. But local brands such as Sunward have recently bridged the gap, offering 40% cheaper waterproofing rated to IP67.
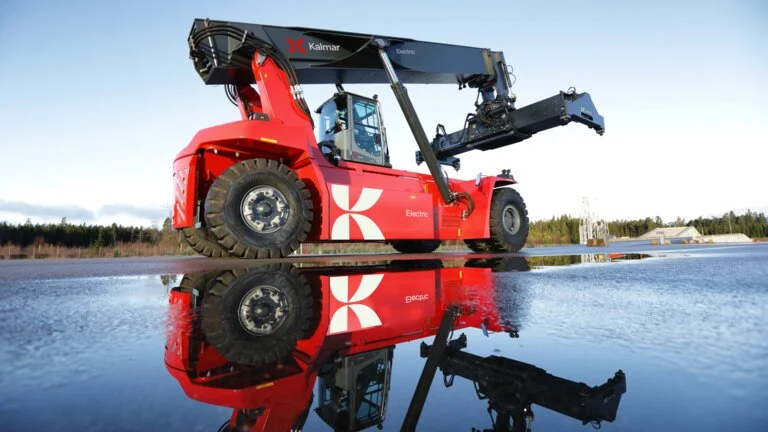
Contents
The Ultimate Challenge: Vibration Resistance
The real test? Vibration. During its 2023 port automation upgrading project at Ningbo Port, the units of Siemens lasted 12,000 hours before servo motor errors occurred, whereas Sunward needed recalibration every 8,000 hours. But here was the twist: Sunward’s modular design enabled 30 percent faster swap-outs during peak tides. As Thomas Edison put it, “The value of an idea lies in the using of it” — sometimes practicality is worth more than prestige.
Coming Up: Why did Swedish-made telescopic arm rails outlast Japanese rivals in Zhoushan’s salt-laden winds…
The boom slide rails are the unsung heroes of reachstackers, carrying tons of cargo but also having to?withstand environmental abuse. In the salt-spray surroundings at Zhoushan Port,?H?gglunds’ galvanized steel rails with PTFE coating from Sweden lasted 18 months, while Japanese competitors’ standard chromium plating lasted half as long. But 2024’s game-changer? Another company is Chinatrack which is based in Guangdong, whose hybrid ceramic-coated rails are 35% less expensive but have proven to be just as corrosion-resistant as the ones trialed in?Shanghai Port.
Here’s what maintenance logs won’t disclose: H?gglunds’ rails need special lubricating oils (indeed, barrel prices here range from about €120 each upwards), while Chinatrack’s hand with?standard greases. For ports such as Xiamen that face a double-whammy?of monsoons and sandstorms, it can become a math issue: a trade-off between initial savings and hours of labor over the longer term.
Coming up: We break down brake systems—why some German hydraulic discs worked and some others flopped, and why most?Italian air-cooled types have thrived…
Container Terminal Braking Systems: A High-Stakes Engineering Challenge
The Humidity Dilemma in Qingdao
Container terminals represent the ultimate stress test for braking systems — imagine stopping 45 tons of cargo on a rain-slicked deck. High-spec German Bosch Rexroth hydraulic disc brakes, precision-engineered components that shouldn’t have required maintenance even with substantial effort, began showing alarming wear rates during Qingdao’s rainy, humid winters. The moisture-sensitive sintered pads absorbed atmospheric humidity, accelerating degradation.
The Drum Brake Alternative
Italian manufacturer Frenoplast’s air-cooled drum systems demonstrated superior performance in these conditions. Their copper-infused linings withstood Jiangsu Province’s 90% humidity without fading, even after 3,000 hard stops.
The Automation Compatibility Issue
However, Frenoplast’s drum systems present a significant operational challenge: they require weekly clearance checks — a deal-breaker for automated terminal operations.
The 2024 Hybrid Solution
Ningbo Port has pioneered a hybrid approach that combines:
- – Rexroth’s wet multi-disc brakes for yard handling
- – Zoomlion’s ceramic-coated rotors for quayside operations
This innovative combination reduced brake-related downtime by 37% last quarter.
Coming next: The challenge of high-dust environment filtration — how a €5 filter upgrade saved Shenzhen Port €250,000 in engine renewals…