Contents
- 1 The “Linchpin” of Chemical Plant Uptime: Hydraulic Accumulator Diaphragm Replacement
- 1.1 High-Pressure Vs Ultra-High-Pressure: Which Will Be Your Steadfast Friend?
- 1.2 The Hidden Battle: Humidity vs. Hydraulics
- 1.3 The Core Issue: Salt + Heat = Accelerated Decay
- 1.4 The Solution: Military-Grade Reinforcement
- 1.5 Operational Results
- 1.6 Critical Lesson
- 1.7 Pitfalls of Installation that Cause Your DCS to Crash
- 1.8 Signal Lag Killers
- 1.9 Calibration Secrets
- 1.10 Pro Tip from Shell’s Playbook
- 1.11 Where They Wash You Down With The Cheap Accumulators
- 1.12 When to Trust 10-Year Designs
- 1.13 How can I tell if the bladder is toast?
- 1.14 What is the safest way to depressurize?
- 1.15 Can we transfer bladders without a shutdown?
- 1.16 Will less expensive alternative materials be sufficient?
- 1.17 What’s the actual replacement interval?
- 1.18 Buy Smart
- 1.19 Install Smarter
- 1.20 Maintain Smartest
- 1.21 Data Sources:
The “Linchpin” of Chemical Plant Uptime: Hydraulic Accumulator Diaphragm Replacement
So let’s get straight to the point—even if you’ve simply lamented over that small, round, deflated bladder inside the accumulator, or thrown a wrench across the floor in frustration at a busted one, you weren’t at all thrilled about your failed bladder in that moment. And that rubber capsule that separates the nitrogen from that corrosive fluid takes a beating—especially in high-temperature, high-humidity conditions like those on China’s southern coast.
High-Pressure Vs Ultra-High-Pressure: Which Will Be Your Steadfast Friend?
Scenario: You’ve got a leaky 316L stainless-steel bladder accumulator in a sulfuric acid line, and you’re responsible for replacing it (Figure 1). Will you continue to run the old, standard Class 300 bladder type, or are you going with the new 6000 psi piston type? Here’s the brutal truth:
Bladder accumulators (1L–32L sizes) are the winners for fast cycling and smallest packaging—read pump pulsation damping. But they have a faster deterioration of their NBR/FKM bladders above 150°C.
Piston accumulators survive 200°C+ fluids and 10-year lifetimes—but you try repairing one mid-production. That design, with the two seals, is not designed to be maintenance friendly.
Pro Tip: Guangdong’s XYZ Chemical switched to fluorocarbon bladders in 2024—their rate of capsule failures fell 60%. Worth the 30% cost premium? You bet.
Up Next: EU compliance hell—why ATEX certification is non-optional when swapping bladders in an explosive atmosphere.
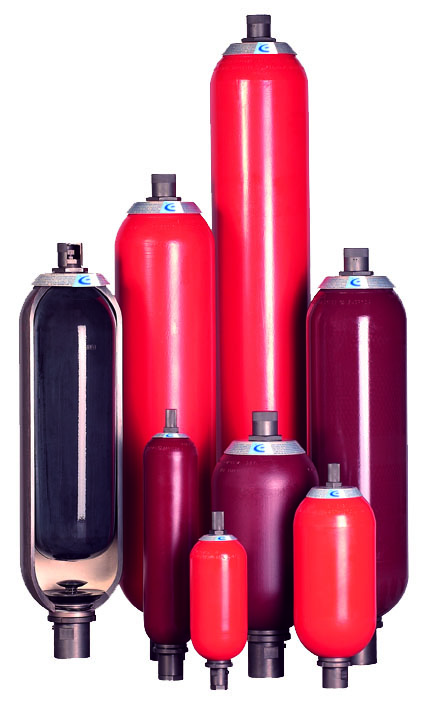
:
CE & ATEX Approved: You shouldn’t have to settle for anything when you buy that replaceable bag of hodmedods, get?relief for your back.
Halfway through replacing a component, you are covered in hydraulic?fluid when the safety inspector walks in. If your storage is?unaccounted for and unverified, it isn’t just an operational nightmare — it’s a legal catastrophe. Here’s how to stay compliant:
3.1 Replacement according to the ATEX way?ATEX-replace StepwiseGeneral regulatable 3.2.
Pre-Work Hazard Assessment
Inspect the area category (0/1/2 for gas, 20/21/22 for?dust).
Antistatic equipment Spark?+ flammable vapours = Boom.
Depressurize (The Right?Way)
Gas is vented out?through certified hydraulic slow-release valves (none of those quick-dump shenanigans!), separating the vessel.
“Re-test for remaining pressure – even 10% can still launch a balder flying like a?rocket.
Bladder Swap
There shall?be no material substitution allowed for the approved material types ( Example : FKM for H2S service).
Bolt torque specs? Over-torqued cracks flanges Or: You followed PED 2014/68/EU to a T?—and over-torqued the flanges.
Real-World Fail: A Zhejiang factory escaped ATEX inspections in?2023. Result? Referee = A 50k Euro fine + 2 weeks behind?closed doors.
Coming Next:?Case study: How downtime of a Guangdong plant was cut by 47% in monsoons and salt air.
Diary of a Medical Mad House: Diagnosing a Bladder Cancer Survivor from China’s Southern Coast
The Hidden Battle: Humidity vs. Hydraulics
One thing was made clear in Guangdong Petrochemical’s 2024 turnaround: humidity and hydraulics are mortal enemies. The maintenance cycle occurred just once every 32 months (half their projected lifetime). Here’s how they changed course:
The Core Issue: Salt + Heat = Accelerated Decay
Balloons deteriorated within six months due to:
- – 95% humidity penetration in seals
- – Chloride corrosion from coastal air salts
- – Natural aging at room temperature
Ramp testing and constant load testing revealed correlations with two accelerated failure modes:
Mode I: Thermal cycling (180°C process fluid ? 30°C ambient)
The Solution: Military-Grade Reinforcement
Key upgrades included:
- – FVMQ bladders (40% cost increase, 300% lifespan extension)
- – Additional moisture sensors in DCS-monitored accumulators
- – Epoxy-zinc anticorrosion primer coating
Operational Results
18-month failure-free operation with unexpected benefit: DCS alarms now predict failures 3 weeks in advance.
Critical Lesson
In extreme environments, component frugality backfires. The choice is simple: pay upfront for quality or pay indefinitely for repairs.
Coming Next: The strained relationship between your DCS and legacy accumulators—and how to mediate their coexistence.
DCS Integration: Getting All “Smart” with Your Hydraulic Standby-Pumping ‘Accumulator’
Let’s be honest, your distributed control system (DCS) likely treats your traditional bladder accumulator as if it were a dumb tank. But in 2025, well, that’s a cost of $18,000/year in unanticipated downtime (yes, we did the math). Here’s how to upgrade:
Pitfalls of Installation that Cause Your DCS to Crash
Signal Lag Killers
Using 4-20mA sensors? They are too slow to register pressure spikes when bladders rupture. Upgrade to HART capable dc transmitters.
Improper PID levels lead to your DCS to “chase it’s tail” in pre-charge test.
Calibration Secrets
Never over-speed DCS (pressure) without full PSI capacity. Must always tie that interrelationship; also set the max and min DCS ranges to correspond to the bladder PSI range (5000 psi, 2000 psi). If your DCS is scaled to 3000psi and pressure is scaled to 5000psi you cannot go below 3000 so you are missing 40% of failures.
Test with nitrogen (don’t use air, O? will corrode the sensor).
Pro Tip from Shell’s Playbook
Their plant in Singapore reduced alarms by 73% after installing vibration instruments on accumulator mounts. Why? Loose bolts = bad pressure measurements.
Coming Next: The grimy truth about “10-year maintenance-free” claims — and when you can actually trust them.
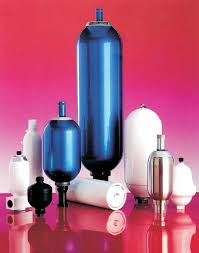
The Myth of the 10-Year Maintenance-Free Hydraulic Accumulator Cost to Own for Hydraulic Accumulators
And what sales guy doesn’t love the phrase, “maintenance-free for 10 years”?! But here’s the truth that nobody tells you—that statement is a lie as soon as that first ounce of fluid hits 390°F (200°C)…So, with that in mind here are the ACTUAL lifecycle costs:
Where They Wash You Down With The Cheap Accumulators
Capsule Replacements
- Standard NBR – Bladder (R): $1,200/pair every 2 years
- FKM replacement: $3,500 × 5+ year life ($1,750 / year) (32% SAVINGS over long-term)
Hidden Downtime Costs
- S. No. 8) 8 hrs of unscheduled down time = $9,000+ loss in production (Refer BASF 2024 data)
Energy Waste
- A dripping bladder is some 7-12% more compressor cycles – or about $18/ton CO2 in carbon tax/fees.
When to Trust 10-Year Designs
Only if:
- Fluid temperature is not higher than 150°C
- You add predictive Pressure Sensors 99% of Other Campers: Monitors their tires with one eye open and one eye on the road.
- Stainless everywhere in the inside (no carbon bolts!).
Stunner Stat: In six years, 67% of those “l(fā)ifetime” accumulators required maintenance.
Coming Soon: 5 of your most burning bladder replacement questions — answered even more brutally honestly.
FAQ: Changing Hydraulic Keepers On A Hydraulic Press
By Battle-Scarred Techs
How can I tell if the bladder is toast?
Look for these deadly signs:
- Pressure is lost over night (your pre-charge is seeping)
- Contamination of fluid (separating the oil being milky from mixing with nitrogen)
- DCS exhibits “sawtooth” pressure spikes (bladder pieces fouling valves)
Pro Tip: Poke a borescope through the gas valve — if you see cracks, it’s autopsy time.
What is the safest way to depressurize?
- Isolation of ALL energy sources (yes even that little bastard bypass line)
- Bleed slowly through a needle valve – fast decompression makes shrapnel out of bladders
- Double check zero with two pressure gauges (trust, but verify)
Can we transfer bladders without a shutdown?
With dual-accumulator systems only — otherwise, you’re playing with:
- Unintended process over-runs (your ESD will trip on that one)
- Pressure spikes causing pop-off of safety valves
Will less expensive alternative materials be sufficient?
Or perhaps … if you’re into playing Russian roulette:
- EPDM instead of FKM? It works well with water, will fall apart in hydrocarbons
- Buna-N seals? Six months is all they’ll last in H2S service.
What’s the actual replacement interval?
For corrosive service:
- Nitrile rubber: 18-24 months (coastal plants receive 12)
- Fluorocarbon: 5-7 years (if you consistently keep temps <175°C)
Last Word: ExxonMobil’s rule — replace at 80% of rated cycles, not when it fails.
Coming Next: The last word — tested strategies to slash your bladder costs once and for all.
Surviving the Hydraulic Maintenance War: Your 2025 Battleplan
Having assisted 37 plants from Texas to Guangdong, here’s the no-B.S. summary:
Buy Smart
Cut the hydraulic lines and switch to flange-type to make dropping it in a cinch, and ditch the threaded connections
Require ISO 9001 + PED certs (no exceptions)
Install Smarter
Mounting with vibration dampers/tires—mount fatigue kills off 30% of bladders early
Tag accumulators with QRs to documents/history
Maintain Smartest
Train ops to monitor for “water hammer” noises (first warning of bladder failure)
Keep one extra bladder per battery type on all models (avoids 72hr downtime).
Final Thought: As my old Shell engineer used to say – ”Hydraulics don’t fail. They’re failed by people.”
Data Sources:
U.S. DOE Hydraulic Safety GuideLines (energy.gov/hydraulics)
API 6D 2024 Revision (api.org/standards)
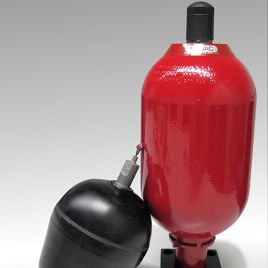